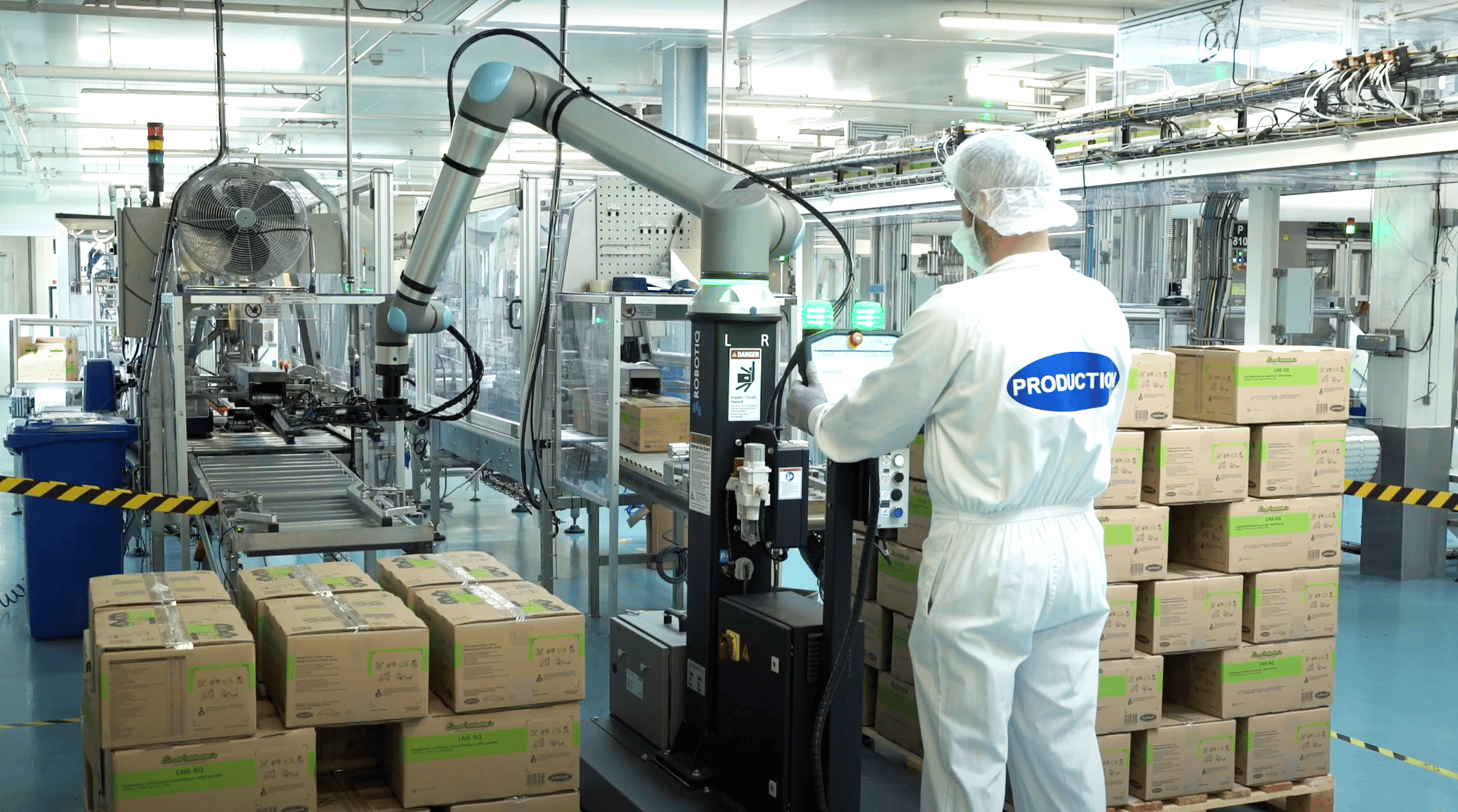
Case Studies
Nutriset
Fueling innovation: Nutriset's automated solution for global nutrition
6 mo
Estimated return on investiment
400
Cartons packed daily
2.20
Meter high pallets
About Nutriset
Nutriset, a leading French company headquartered in Normandy, specializes in the research, development, production, and worldwide distribution of specialized nutritional foods designed to treat and prevent various forms of malnutrition. In response to the challenges posed by the post-Covid era, Nutriset embarked on an automation project to fully automate its production line.
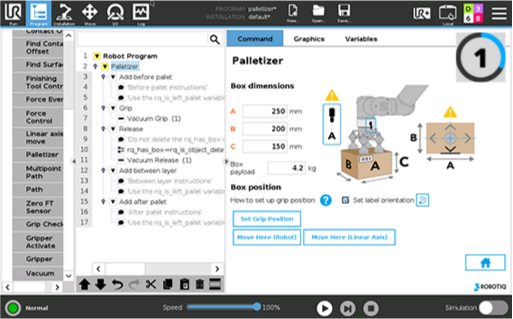
Step 1 - Box dimensions, weight and orientation
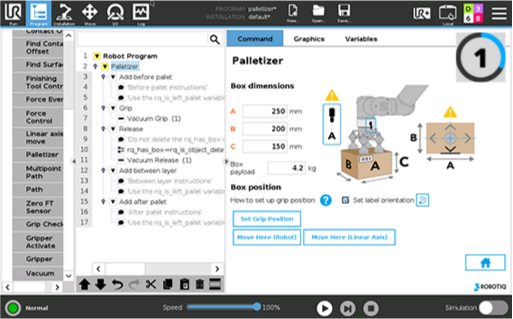
Step 1 - Box dimensions, weight and orientation
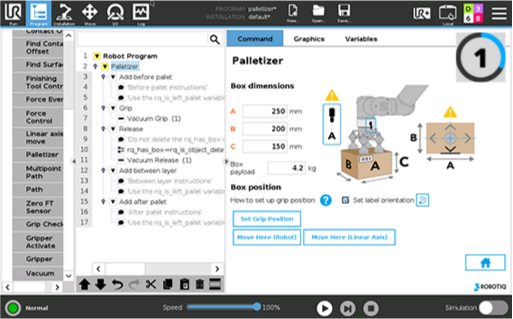
Step 1 - Box dimensions, weight and orientation
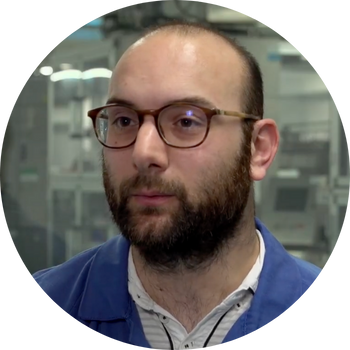
The Problem
Manual post-Covid palletizing posed major challenges for Nutriset. Keen to fully automate its production line, Nutriset faced obstacles such as inconclusive tests due to high payload requirements, limited space, low ceilings, heavy and oversized cartons, as well as pre-cuts on the cartons, which made the process even more complex.
The Solution
While initial trials were inconclusive, the breakthrough came with Robotiq's Palletizing Solution paired with the UR20, which offered the necessary collaborative solution without the need for safety cages making it 100% collaborative. Leveraging Robotiq's expertise and team, Nutriset found the ideal automation configuration to efficiently streamline its palletizing process.
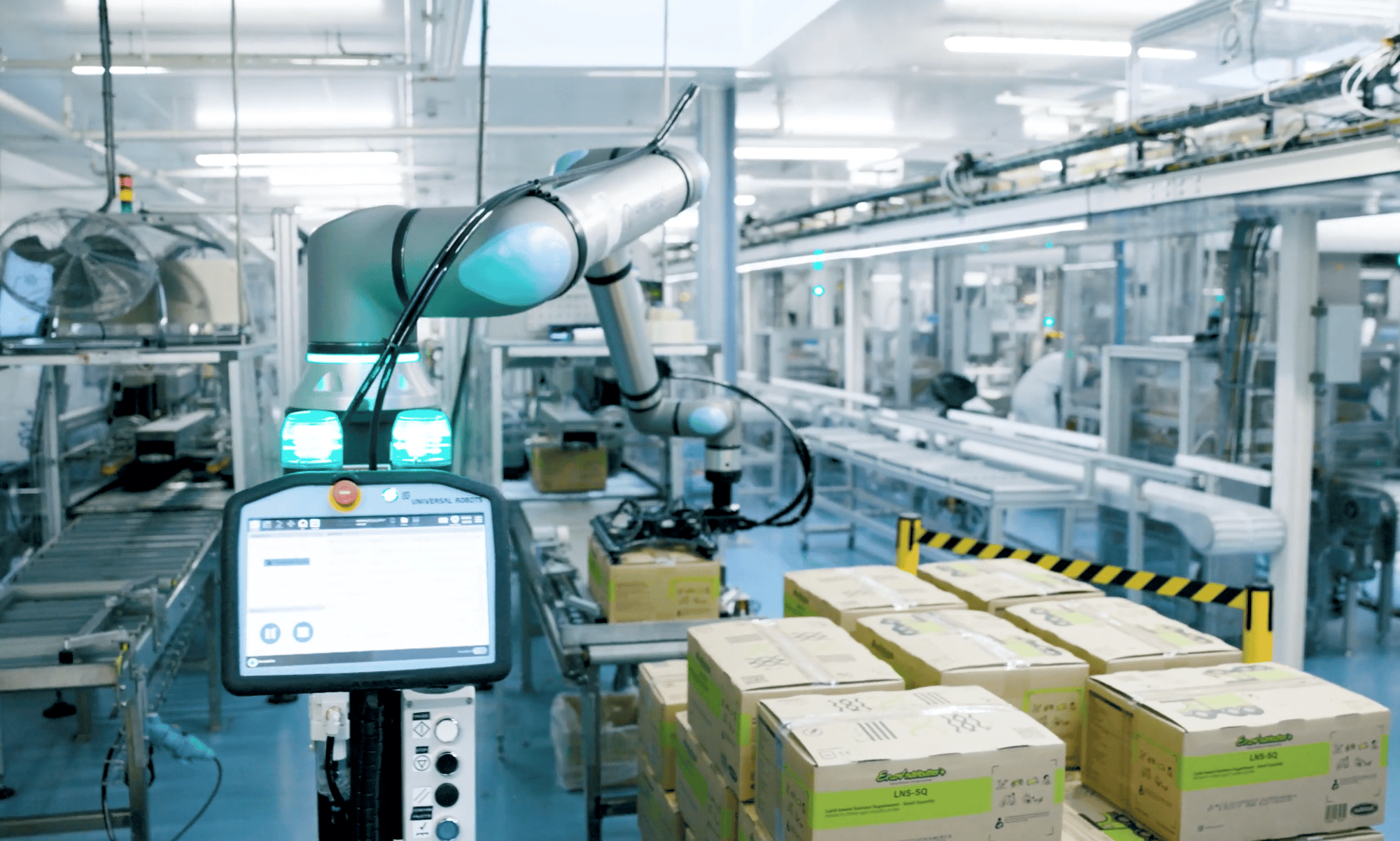
Convincing wins.
Robotiq’s palletizing cobot brought benefits on many levels:
- Reduced musculoskeletal disorders (MSDs): Significant reduction in repetitive strain injuries associated with palletizing tasks, resulting in a healthier workforce.
- Increased productivity: Improved operational flexibility and reduced downtime have led to substantial productivity gains, streamlining all processes.
- Rapid return on investment: The rapid integration of the automated solution resulted in an estimated return on investment of 6 months.
The Robotiq solution
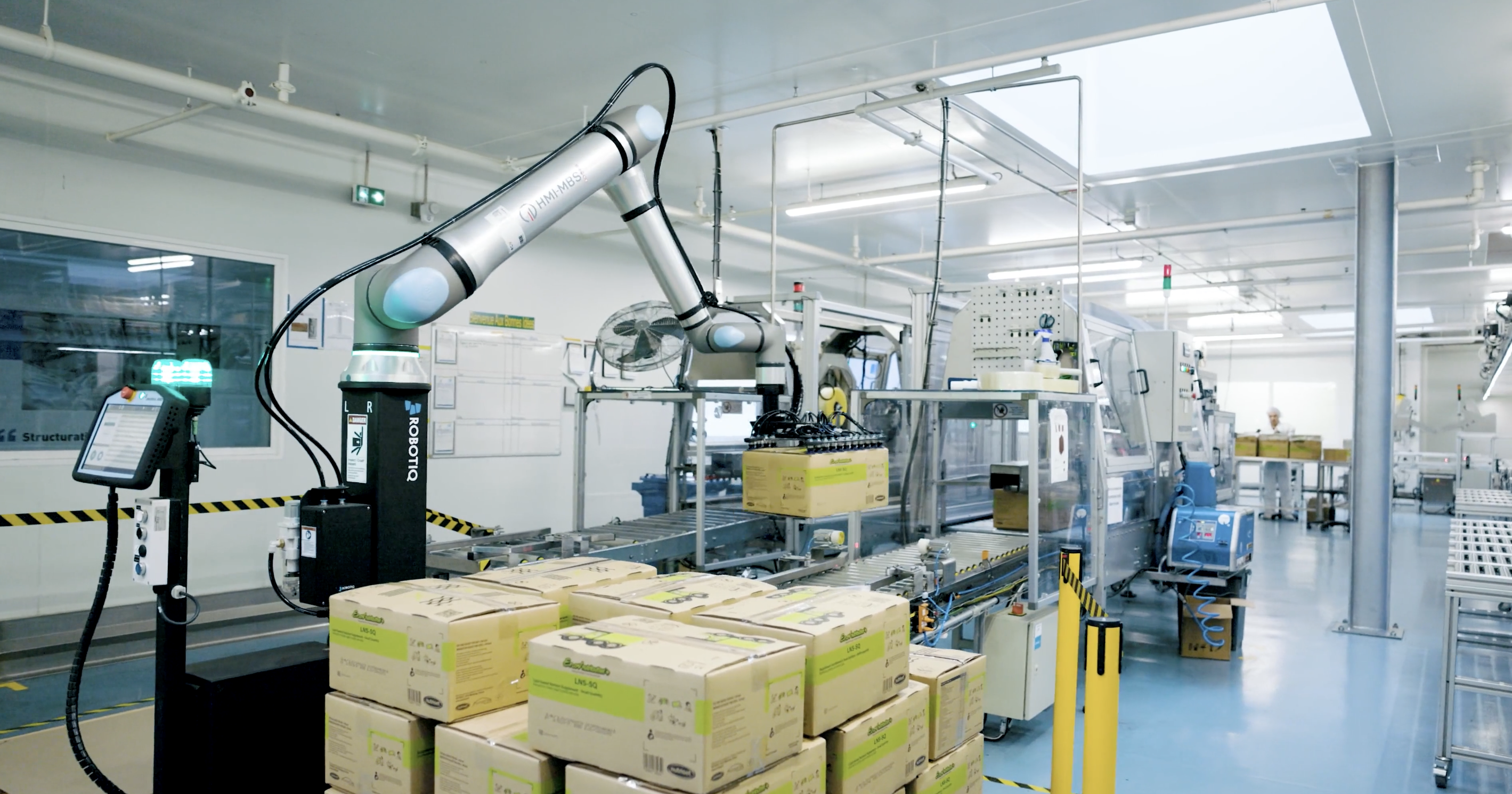
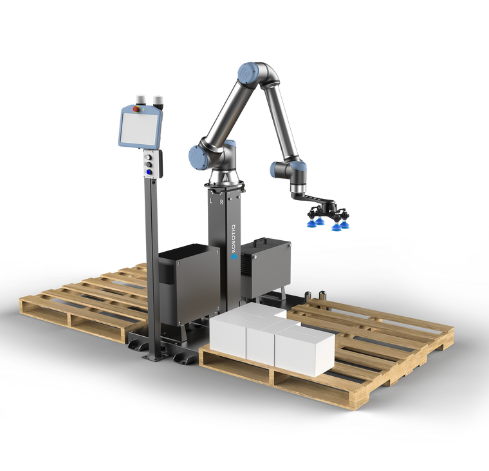
Palletizing
The Robotiq Palletizing solution transformed Napco’s operations: not only did it lead to a 15% increase in production, but it also reduced the risk of injuries and allowed the company to reallocate eight workers per day to more specialized tasks.