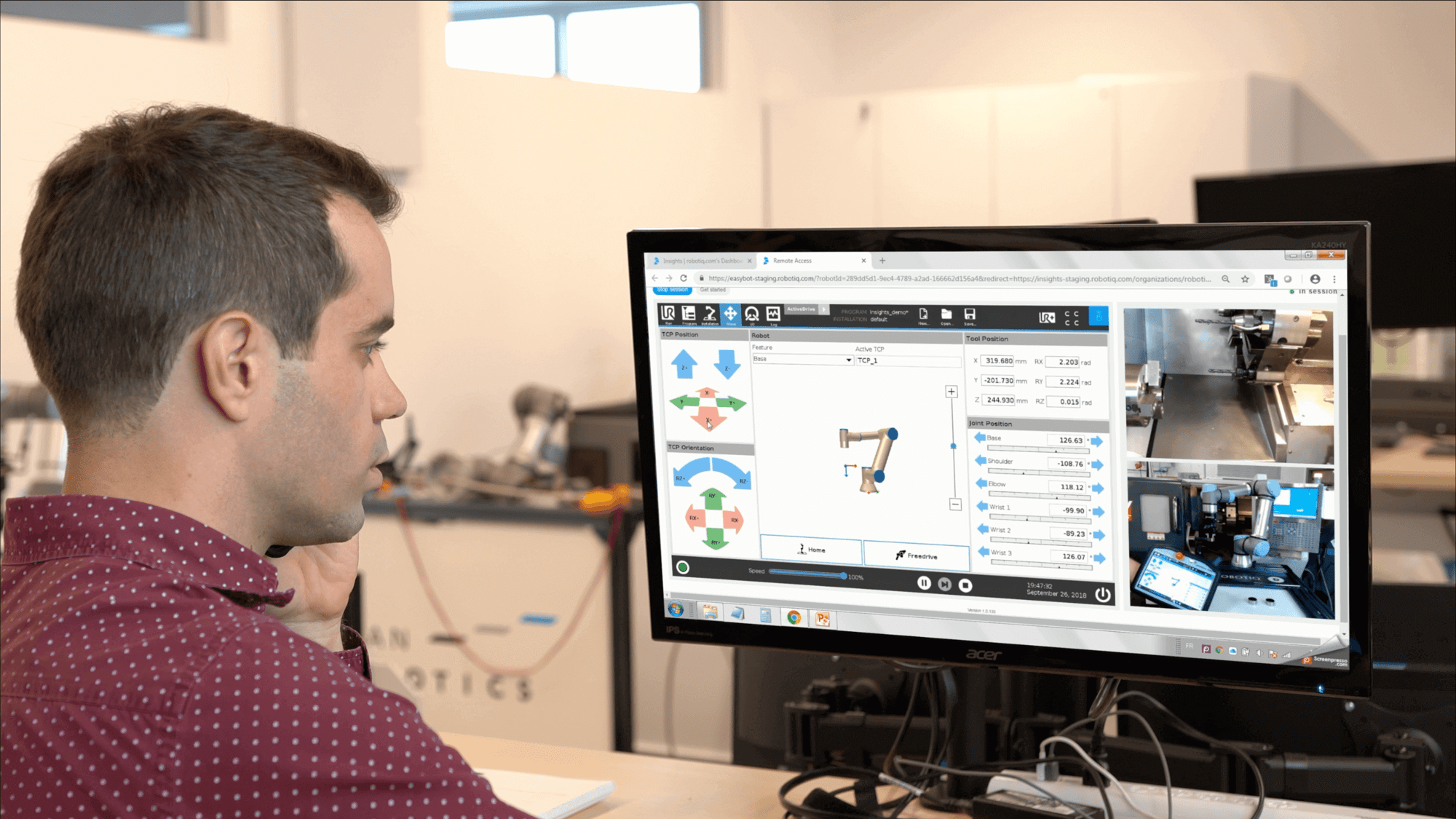
Get the Answers You Need:
Robotiq Frequently Asked Questions
Palletizing Solution
For the AX10 and the PE10, there are three ways to move the solution in the factory during the initial installation. First, we provide wheels that you can easily install on the base, so you can move it freely. Second, the base and axis are also equipped with lifting eyelets, which you can use with a lifting harness. Finally, you can simply move the solution with a forklift.
Keep in mind that these methods are not suitable for moving the palletizer from line to line in operation mode or when a washdown is required.
For the PE20, the palletizer is equipped with fork slots / pockets to make it easier to move during installation.
We provide concrete anchors for attaching the base to the ground, but you could also use your own anchor or clamping solution.
Yes, it’s possible to palletize more than one SKU. For example, you can palletize SKU A on the left pallet and SKU B on the right pallet. elementum tellus.
Yes, as long as they have the same box height.
For the AX Series, the movement of the cobot and 7th axis is optimized for performance, so the palletizer cannot be used in a collaborative mode (that is, with a human operator right next to it). Safeguarding of the palletizer is therefore required. Unless the project is delivered via Robotiq’s Installation Services, the customer is responsible for doing a proper risk assessment and implementing safety measures before going into production.
The PE Series solutions have no linear axis, so they are more easily used in collaborative operations. In all cases, a proper risk assessment is required.
Yes. In the Palletizer node tree, you can define between-layer operations in the Between layers folder. You can also use a linear axis move node to help program those tasks. As such, even if we are not providing any hardware/software to manage interlayers, our system can accommodate a custom interlayer system.
The delivery timeline for the solution varies based on several factors. If shipped without the UR robot, it can be dispatched within 14 days. However, if it includes a UR robot, the shipment time may vary.
For installation, it depends on whether you opt for our installation services, a do-it-yourself approach, or external System Integrators (SIs). Each of these options has its own time frame, which may be adapted to suit your specific needs and circumstances.
Yes, it is possible to work with other types of parts and packaging, such as shrinkwrap and plastic buckets, as long as they’re stackable and can be picked using a vacuum gripper or mechanical gripper. It is also possible to palletize open-top boxes and trays with a custom gripper.
Got unanswered questions?
Contact us now!
Machine Tending Solution
Yes, the solution and software can manage two CNCs—but not simultaneously. The robot can be moved from one CNC to another CNC. You can leave the grippers on the robot, but you’ll need a pneumatic panel and Robotiq controller on each CNC.
Use the following link to get a quote and see what’s included in the Machine Tending Solution. Configuration options vary depending on your CNCs.
Got unanswered questions?
Contact us now!
Screwdriving Solution
The screwdriver is only compatible with Universal Robots, specifically UR3 to UR16, E-series and CB-series.
The screw feeder has no restrictions; it can theoretically be used with any robot or screwdriver on the market. Note that it was designed and optimized to work with the Robotiq Screwdriver SD-100.
Possibly, if…
1. The screw feeder is for an automated process and the screw is picked from the top (not pulled laterally).
2. The IOs are configured the same way.
3. The vacuum sleeves can access the pick location.
No. The Robotiq URCap is only compatible with the Robotiq Screwdriving Solution.
Possibly, depending on the screws. Using the same screwdriver for two different screws while in operation requires using the same bit, vacuum sleeve, and vacuum adjustment. A good example of when this would be possible is when you have two identical screw heads but with different lengths.
Yes, the screwdriver can be used with a tool changer. However, the screwdriver does not use the standard UR wrist connector (M8 12-pin) for electrical wiring, so the tool changer must be able to accommodate a 5-pin / 2-amp connection in order to be able to use more than one screwdriver per robot.
The cycle time depends on the application, including factors like the number of threads, tool RPM, screw insertion strategy, and robot movements. With a good cell layout where the feeder and fixtures are nearby, and with a typical 7 threads of engagement, the overall pick and screw cycle time can be as fast as 6 seconds per screw.
Got unanswered questions?
Contact us now!
Adaptive Grippers
Yes, the adaptive grippers can be used on other robot brands.To know if Robotiq Adaptive Grippers are compatible with a certain brand, you should ask for the robot bolt pattern or model, and the communication protocol. Don’t hesitate to connect with a Robotiq expert. We will be happy to assist you.
Here is the precise payload for each Robotiq Adaptive Gripper:
Hand-E: 5 kg in Form-Fit and 4.7 kg in Friction mode
2F-85: 5 kg in Form-Fit and in Friction mode
2F-140: 2.5 kg in Form-Fit and in Friction mode
3F: 10 kg in Form-Fit mode and 2.5 kg in Friction mode
The maximum operating temperature is 50 degrees Celsius (122 degrees Fahrenheit). Operating the equipment at a higher temperature might damage the Gripper and the warranty will not apply.
Got unanswered questions?
Contact us now!
Vacuum Grippers
Yes, it is available on Universal Robot with a URCap and Techman Robots (TM-Omron also) with dedicated TMComponents. Other Tomahawk robots such as Hanwha, Doosan, Aubo, and Yaskawa do not have a UI or plugin to control the grippers. Use the same procedure as if they were standard industrial robots.
The quality of the entry air will greatly influence how frequently the internal (replacement) filters have to be replaced. Typically every six (6) months when running two (2) shifts per day.
EPick is connected on cobot wrist for Universal E-Series. It requires no air supply, is easy to handle and allows optional suction cups configurations.
Got unanswered questions?
Contact us now!
Force Torque Sensor
The “recommended minimum threshold” represents the smallest variation of force or moment that the sensor can detect reliably (without filtering) when installed on a robot.
For the FT 300-S, like many sensors available, the noise level exceeds the resolution, which is why the noise specification is emphasized rather than the resolution. This is because the noise, rather than resolution, is the limiting factor in its applications.
Generally, the FT 300-S is immune to external electrical noise. This means that the quality of the signal is not affected by other industrial equipment located around the robot. The increased sensitivity of the Sensor improves the results for applications such as product testing, assembly and force processes, regardless of the industrial equipment around the Sensor.
Sensor noise is the most important metric for achieving successful hand guiding and valuable force control.
The FT 300-S’s accuracy allows to perform most of the product testing, assembly and force processes. Also, it should be noted that for most applications, sensitivity and repeatability is more important than accuracy.
Got unanswered questions?
Contact us now!
Wrist Camera
The Robotiq Wrist Camera is a state-of-the-art vision system designed to be mounted on robotic arms. It simplifies robotic applications by enabling automated systems to see and adapt to varying environments. This enhances manufacturing processes by improving precision, reducing setup time, and increasing overall efficiency, aligning with the goal of maximizing productivity.
The Robotiq Wrist Camera enhances workplace safety by enabling robots to perform complex, repetitive, or hazardous tasks with high precision, minimizing the risk of accidents and injuries. This aligns with Robotiq's commitment to putting people first, ensuring a safer and more efficient working environment.
The Robotiq Wrist Camera stands out due to its ease of integration, user-friendly interface, and ability to adapt to a variety of tasks without extensive programming. Its compatibility with the Lean Robotics Methodology of Design, Integrate, and Operate, ensures a streamlined and efficient deployment, making it a top choice for manufacturers seeking to enhance productivity and adaptability in their operations.
Got unanswered questions?
Contact us now!
Sanding Kit
No, only available on Universal Robots for the moment.
A Pneumatic Orbital Tool, a Bracket, Sanding Media, a Finishing Copilot, a Quick Start Guide, Air Control Accessories.
Robotiq Sanding Kit can handle Wood, Plastic, Metal, Fiberglass, Solid Surface, Carbon Fiber.