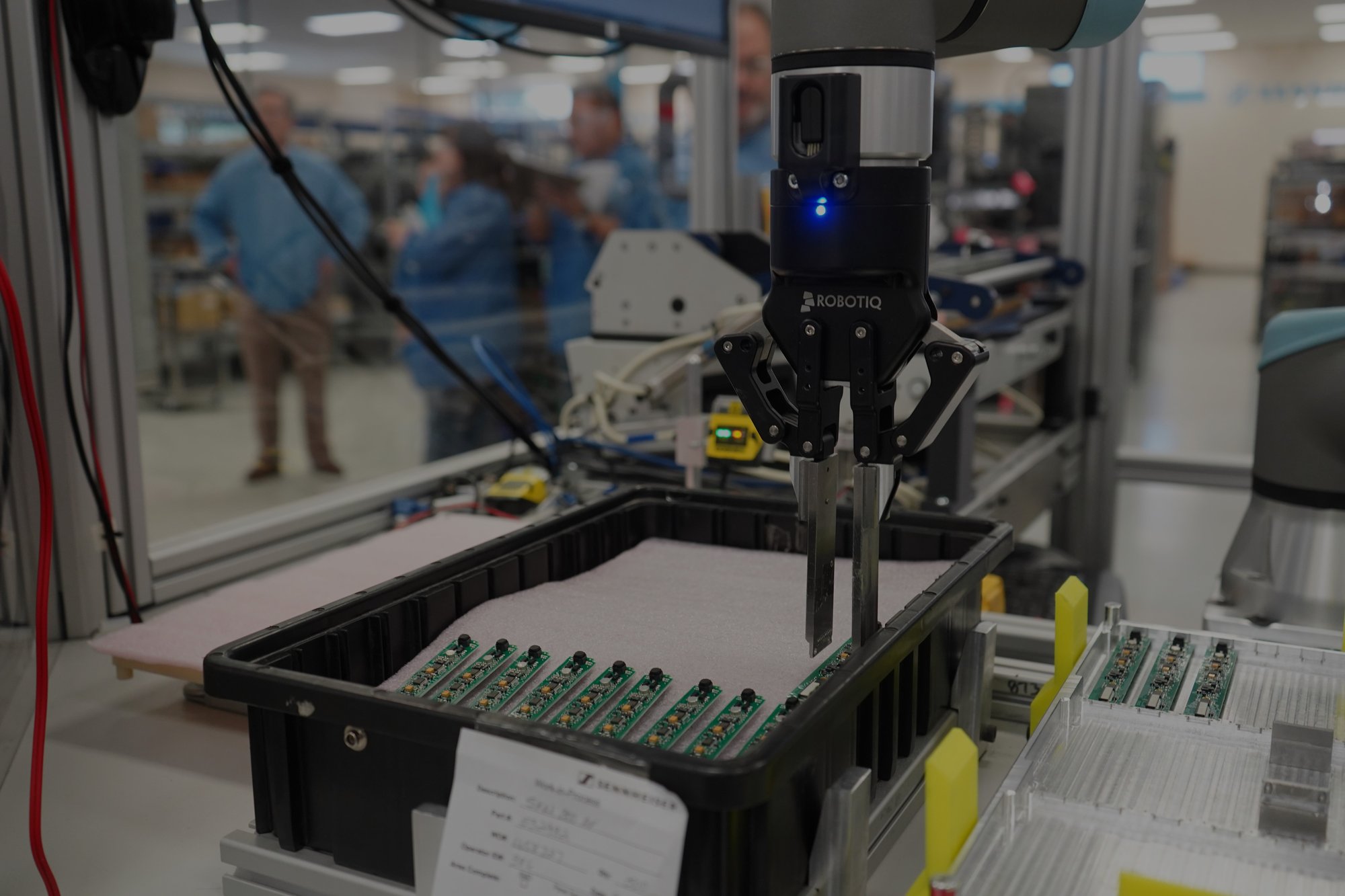
Case Studies
Sennheiser
Increase quality testing numbers
33%
More unit tested
115
Printed Circuit Board inspected
30 000
Pieces assembled per day
About Sennheiser
Sennheiser Manufacturing USA produces professional audio equipment for the Americas and Asia. Manual, meticulous testing of printed circuit boards (PCBs) became a bottleneck on the production floor.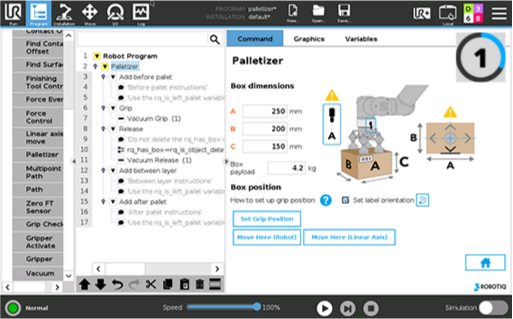
Step 1 - Box dimensions, weight and orientation
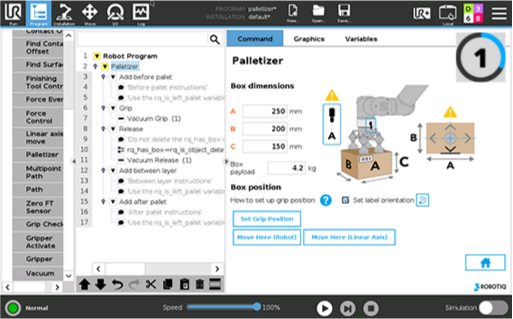
Step 1 - Box dimensions, weight and orientation
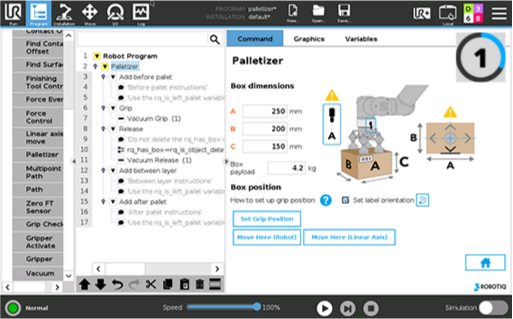
Step 1 - Box dimensions, weight and orientation
Sennheiser USA Picks 115 different types of PCBs with an Adaptive Gripper
The cobots are fast, but I can keep up - and it’s great how much we’ve increased our numbers
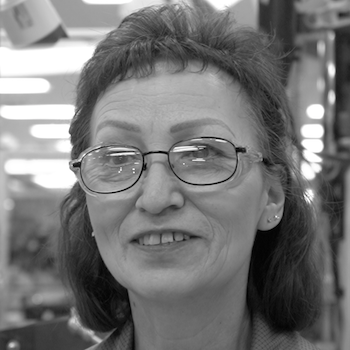
Marcella Segovia
PCB Testing Operator, Sennheiser Manufacturing
Overcoming Challenges: Our Solutions
The Problem
Sennheiser Manufacturing USA produces professional audio equipment, which involves assembling thousands of different PCBs. Their meticulous process of manual PCB testing became a bottleneck on the production floor.The Solution
Sennheiser used Robotiq’s 2F-85 Adaptive Gripper to handle 115 different PCBs and saw a 33% increase in the number of units tested. They also used Robotiq Insights to track daily production metrics, and the resulting data helped justify adding a second Universal Robots cobot in the summer of 2019.The Robotiq solution
Four Robotiq Machine Tending cells were deployed at Fusion OEM within less than a year. A process made easy thanks to the use of Force Copilot.
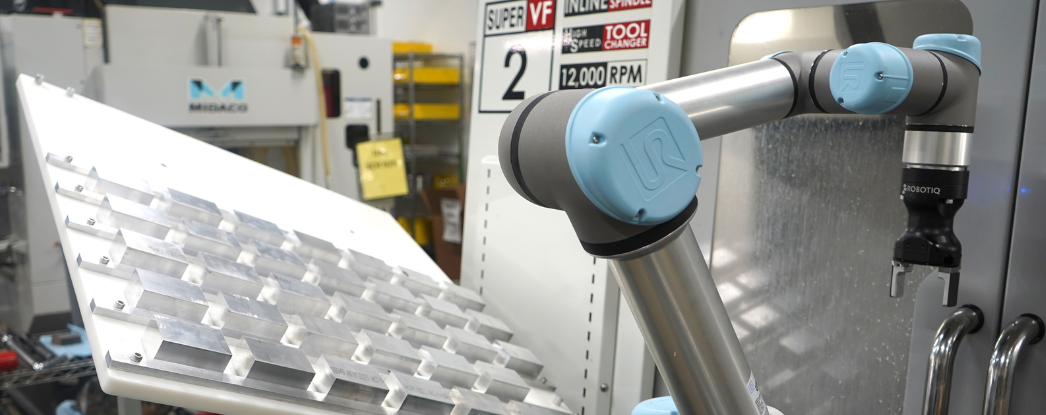
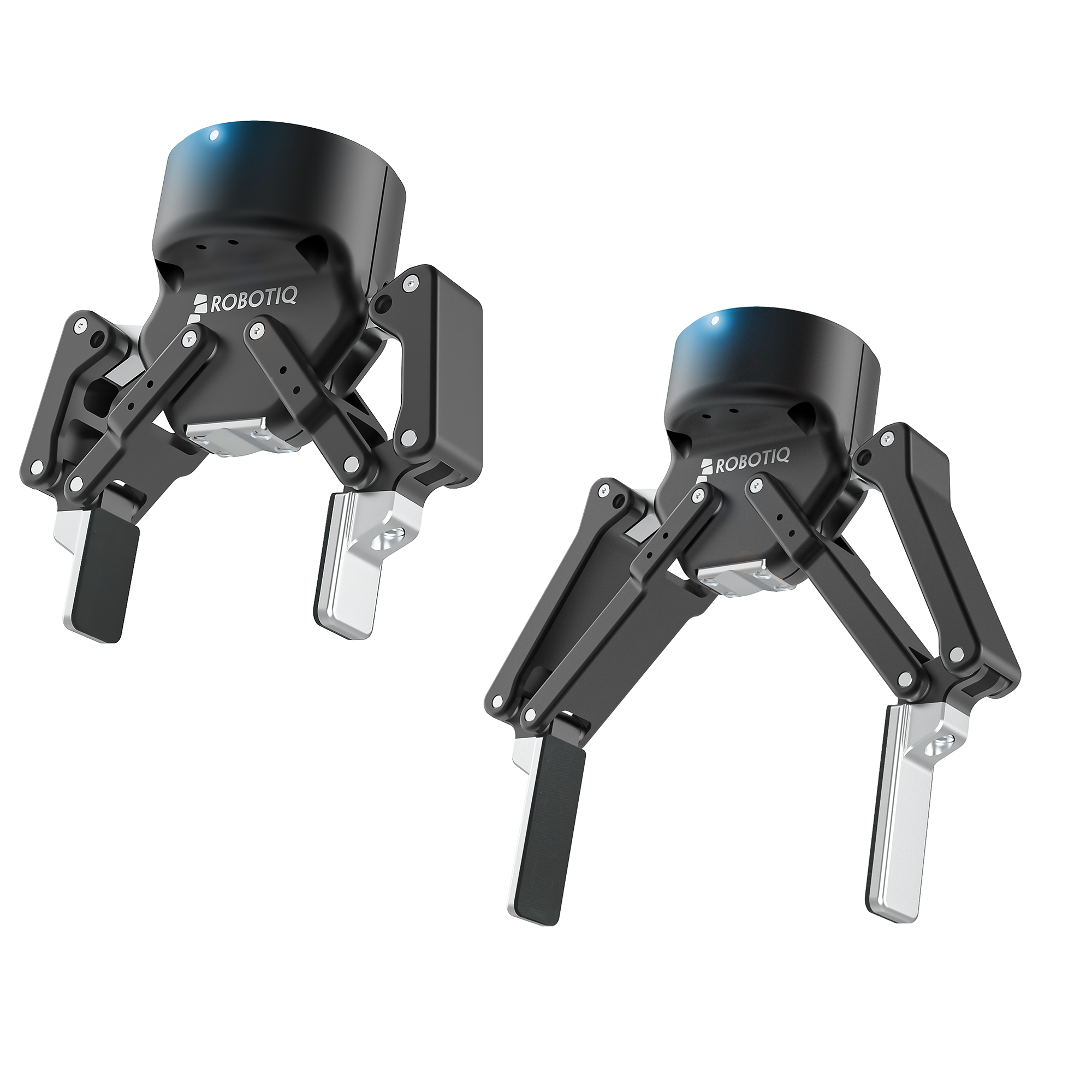
Products
2F-85 adaptive gripper
The 2F-85 Adaptive Gripper allowed Sennheiser to manage part changeovers quickly, which was important for their high-mix, high-volume production.