.jpeg?width=2000&name=2F85-Wrist-Camera-Machine-Tending-Walt-Machine-58%20(1).jpeg)
Robotiq Machine Tending Solution
Maximizing CNC machine productivity through simplified robotic automation
The Problem
CNC underperformance
Machine shops typically operate CNC machines at only 60-70% capacity. Wasting 30% of runtime can lead to revenue losses. This underperformance is mainly due to a shortage of skilled operators, caused in part by a general disinterest in repetitive and low-skilled jobs. Plus, robotic automation's perceived complexity and costliness are deterrents for many businesses.
The Solution
Maximize efficiency
A robotic machine-tending solution can increase productivity rates, giving shop owners the opportunity to empower their existing workforce to take on more added-value tasks. Machine-tending automation has become simpler since the advent of collaborative robots. It boosts consistency and guarantees product quality.
Presentation
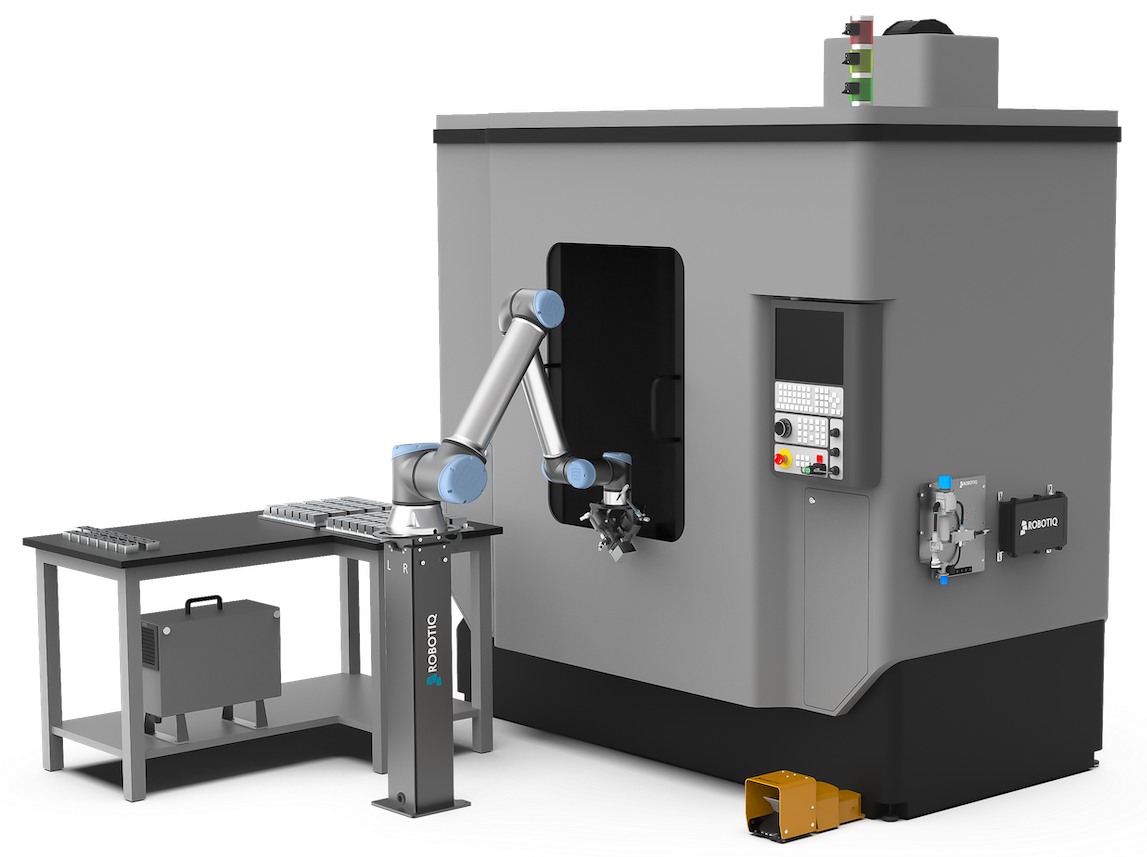
Relentlessly load and unload your machine
The Robotiq Machine Tending Solution is a low-risk and cost-effective system to quickly automate the loading and unloading of CNC milling and lathe machines.
With a one-year ROI, Robotiq's solution helps recover lost CNC runtime. Robotiq's approach streamlines the automation process by eliminating the need for custom programming or permanent modifications to the CNC machine control panel. The hardware and software components included in the Robotiq Machine Tending Solution are connected independently from the CNC machine and programmed to mimic the actions of a skilled operator.
Robotiq's difference
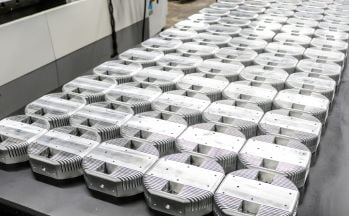
Boost productivity

Automating machine-tending operations enables one operator to handle quality control and part management for multiple cobots. This allows your staff to engage in greater value-added tasks, which increases overall labor effectiveness (OLE) by making the best use of high-performing personnel.
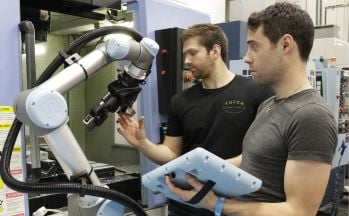
Empower your workforce

Robotiq’s solution lets you refocus skilled employees in areas of high-value tasks that offer autonomy and variety. The configurations are user-friendly, empowering your workforce to develop new skills. Plus, programs are created 75% faster than with traditional programming.
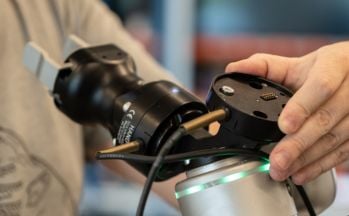
Promote adaptability

The solution's proven and standardized approach speeds up implementation by addressing complex issues ahead of time. It guarantees compatibility with all machines, regardless of model, type, or age—and it simplifies scaling by offering a universal solution, language, and training.
Discover what the Robotiq Machine Tending Solution can do for you
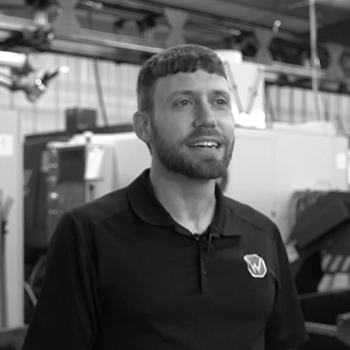
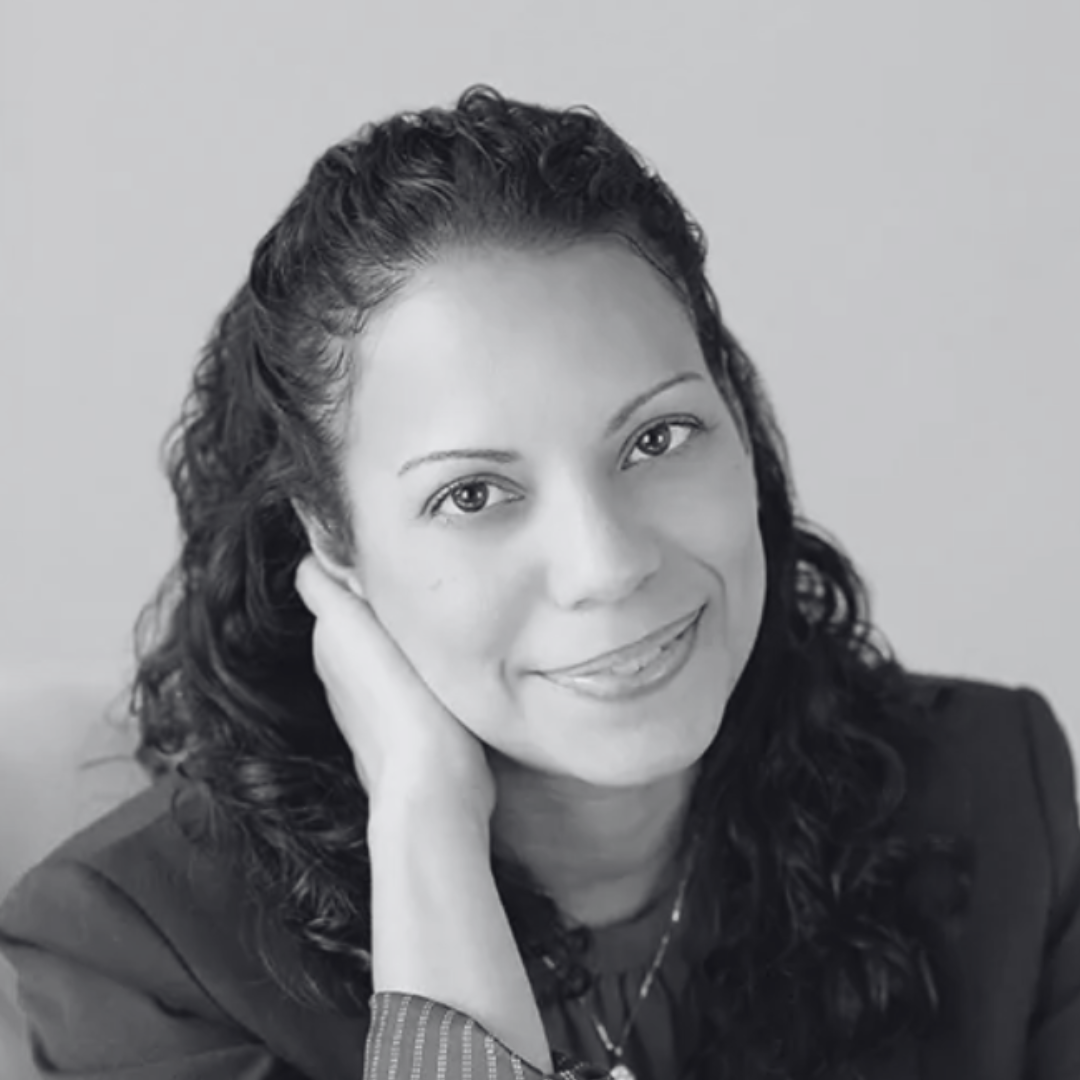
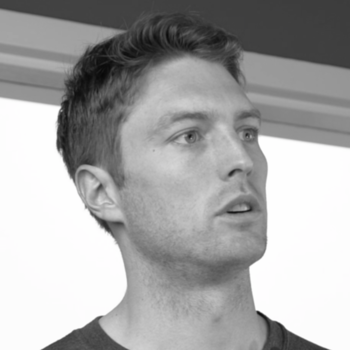
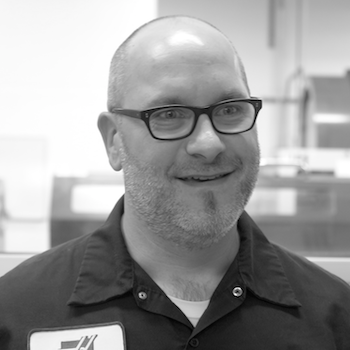
Specs & components
Air supply connection type | BSPP 3/8 in female (adapter to NPT 3/8 in male provided) |
||
---|---|---|---|
Minimum required air flow | 400 l/m (14.1 cfm) at 6 bar | ||
Required media (compressed air) | ISO 8573-1 class 7.4.4.1 | ||
Nominal supply voltage | 24V | ||
Type of source | DC | ||
Grip force | 20 to 180 N | ||
Hand-E IP rating | IP67 | ||
Part weight (max) w/ Single Hand-E EoAT |
UR5e 3.9 kg (8.6 lb) UR10e & UR20 5 kg (11 lb) |
||
Part weight (max) w/ Dual Hand-E EoAT |
UR5e 1.3 kg (2.8 lb) UR10e & UR20 2X 5 kg (11 lb) |
||
Hand-E max part size | Up to 127 mm (5 in.) |
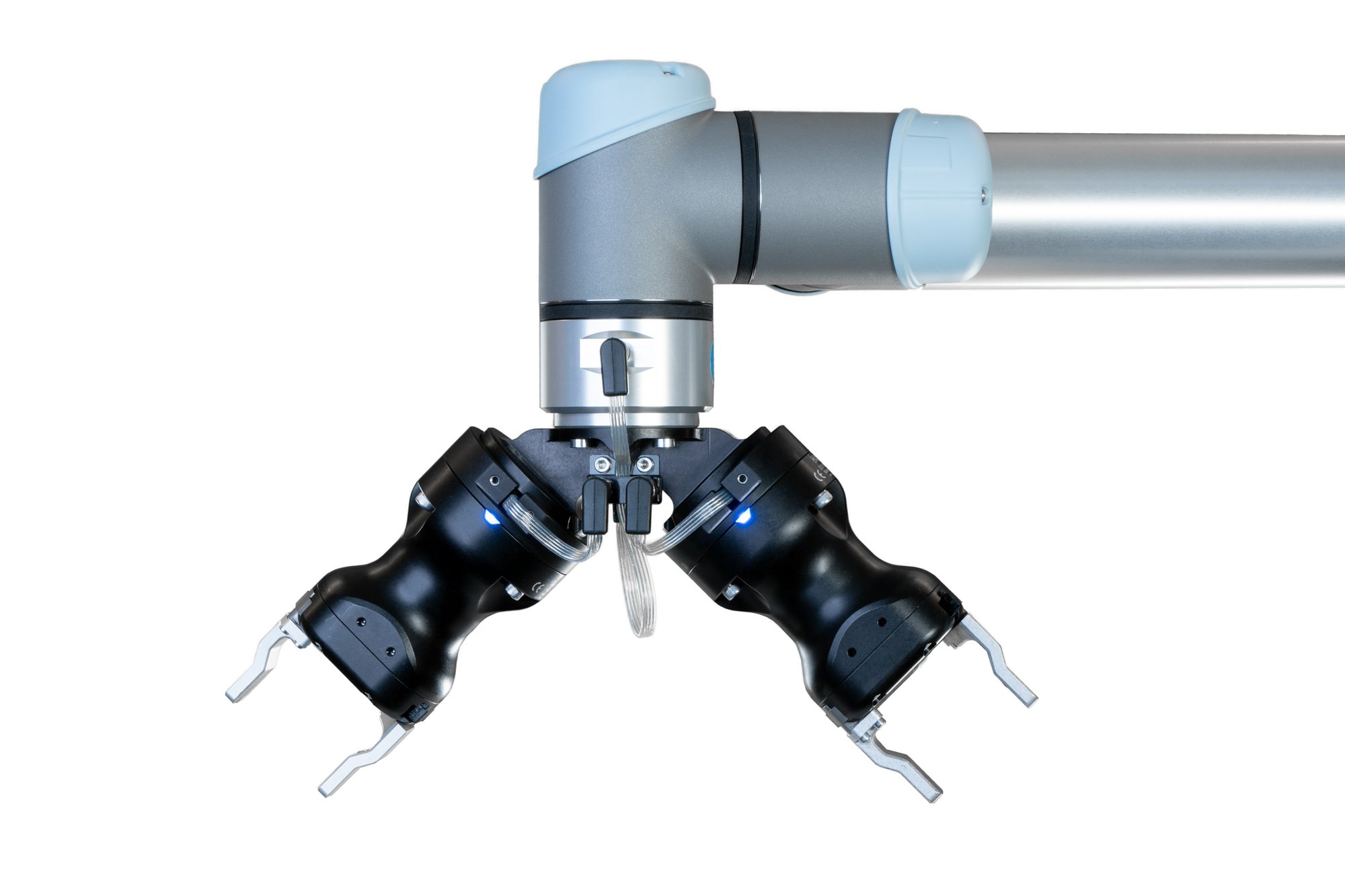
Hand-E adaptive grippers
The Hand-E adaptive grippers are grippers whose fingers are actuated by a single motor. They can execute several machine-tending tasks, such as handling parts, positioning parts in the workholding device, and opening and closing the machine door. They can be configured in single or dual mode.
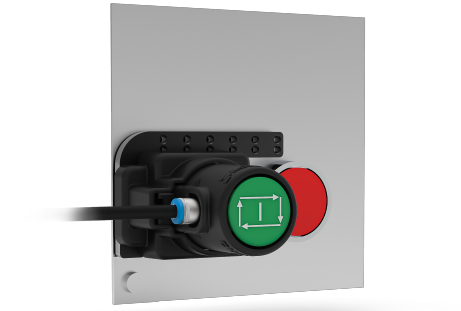
Button activator
The button activator is a pneumatic actuator whose mechanical motion can activate different types of control components. It’s typically installed on the control panel’s “Start Cycle” button to start the machine cycle, or on any other button that activates a device. Additional button activators can be purchased separately.
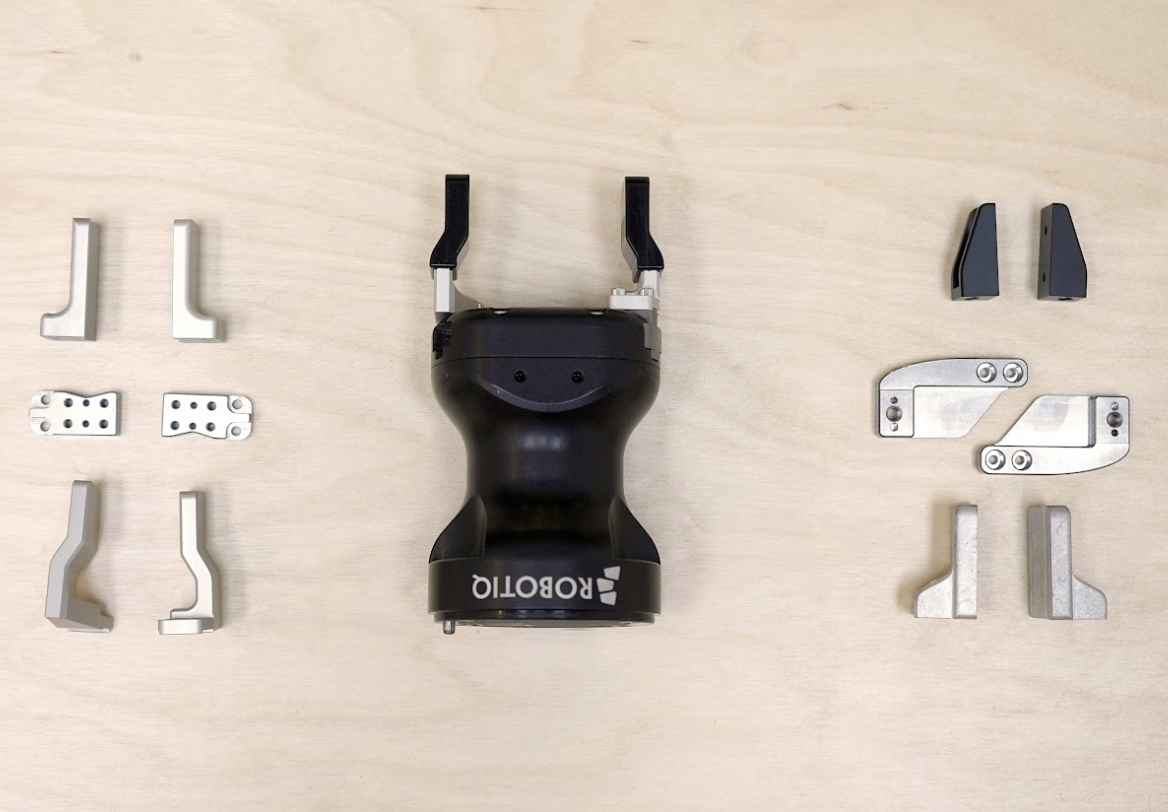
Fingertip kits
Fingertips are mechanical assemblies installed on the Hand-E gripper. The solution includes axial, radial, and prismatic sets of fingertips to ensure a secure grip with different part sizes.
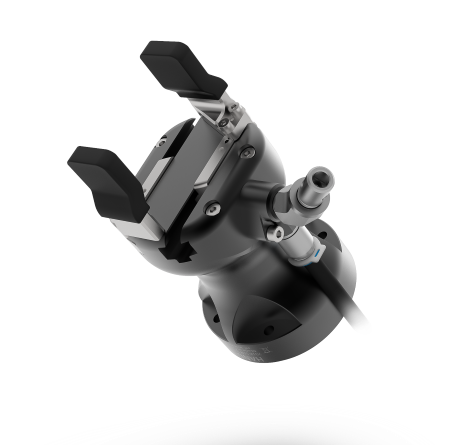
Air nozzle
The air nozzle is designed to conduct compressed air. It is attached to the Hand-E gripper and can be positioned at various angles.
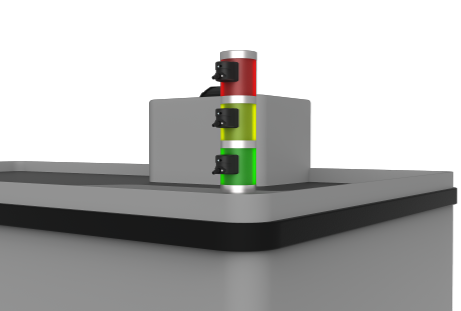
Multichrome signal light detector
The Robotiq Machine Tending Solution relies on intelligent sensors to connect to the CNC machine. These sensors communicate with the CNC machine by reading and signal light colors and frequencies. Designed to be attached directly to the signal lights, these sensors send converted electrical signals via electrical cables.
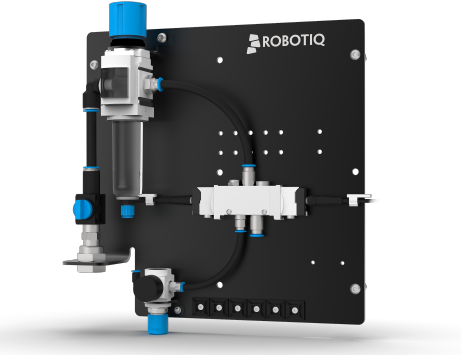
Pneumatic panel
The panel includes the valves and regulators required to operate the air nozzle and button activator.
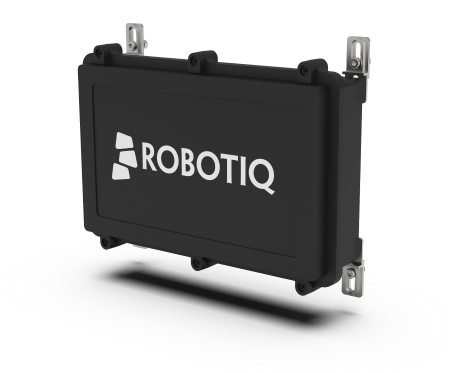
Robotiq controller
The Robotiq controller is packed with advanced engineering, so you only need to focus on simple configurations to get the solution running. The controller manages the Robotiq Machine Tending Solution’s modules and provides a simple and optimized link with the Universal Robots controller.
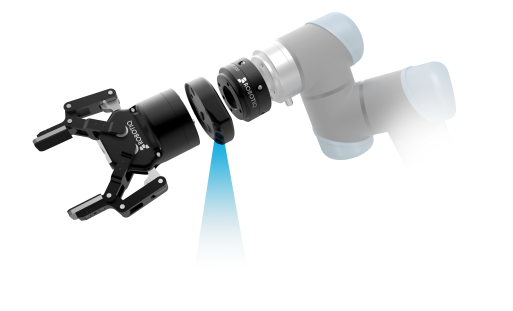
Wrist Camera (optional)
The Wrist Camera handles a wide range of parts. It reliably detects objects regardless of the background or lighting. The user-friendly software and visual interface walks the user through the configuration process in just minutes. No expertise in robotics or vision systems required.
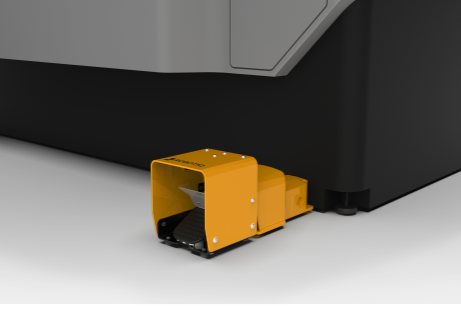
Footswitch activator (optional)
The optional footswitch activator is used to open and close the vise of lathe CNC machines. It comes equipped with pneumatic components (valves and tubes).
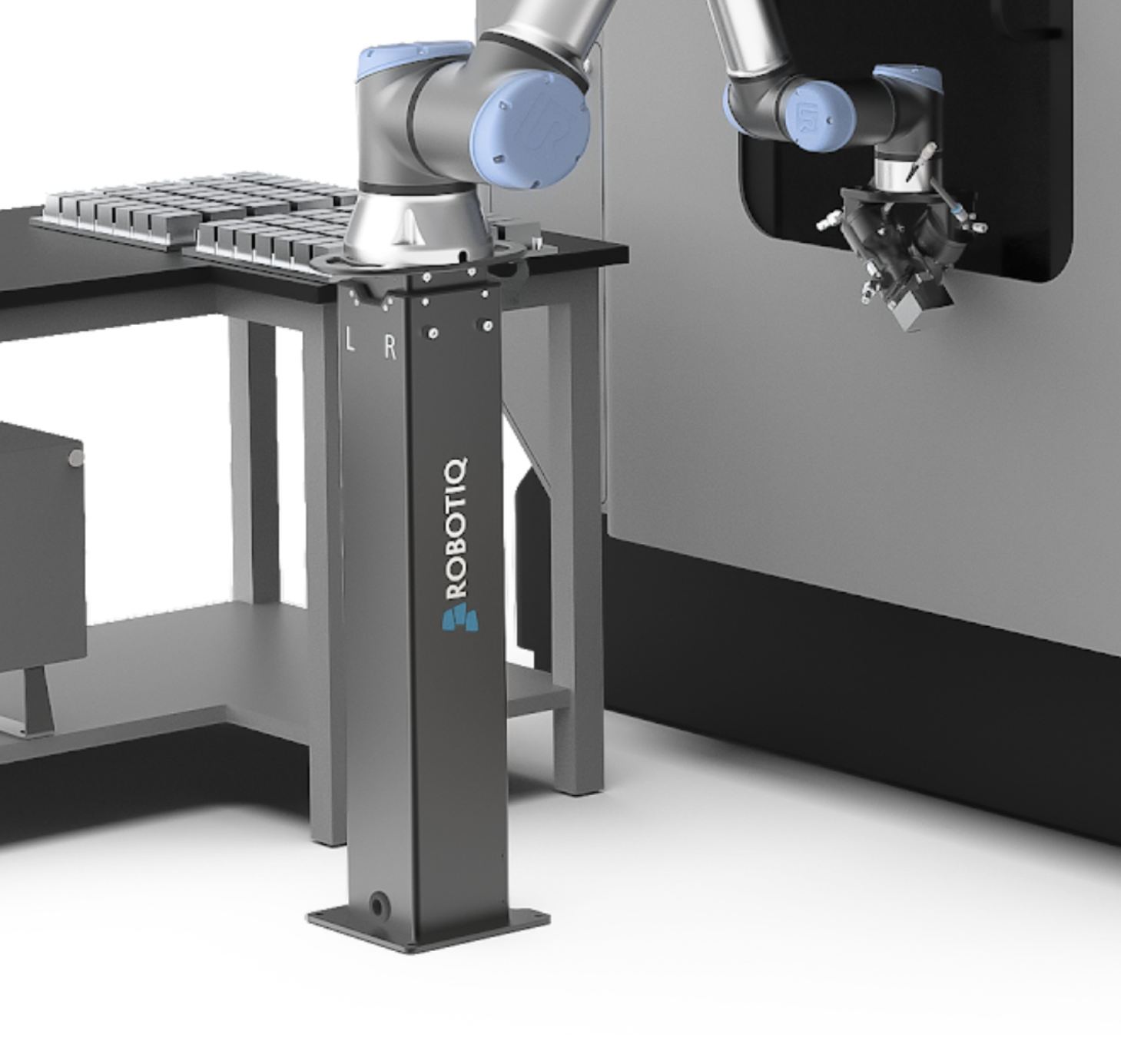
Adjustable pedestal (optional)
The pedestal is a solid metallic and hollow column. The pedestal's height can be adjusted to 13 different positions manually.
Software
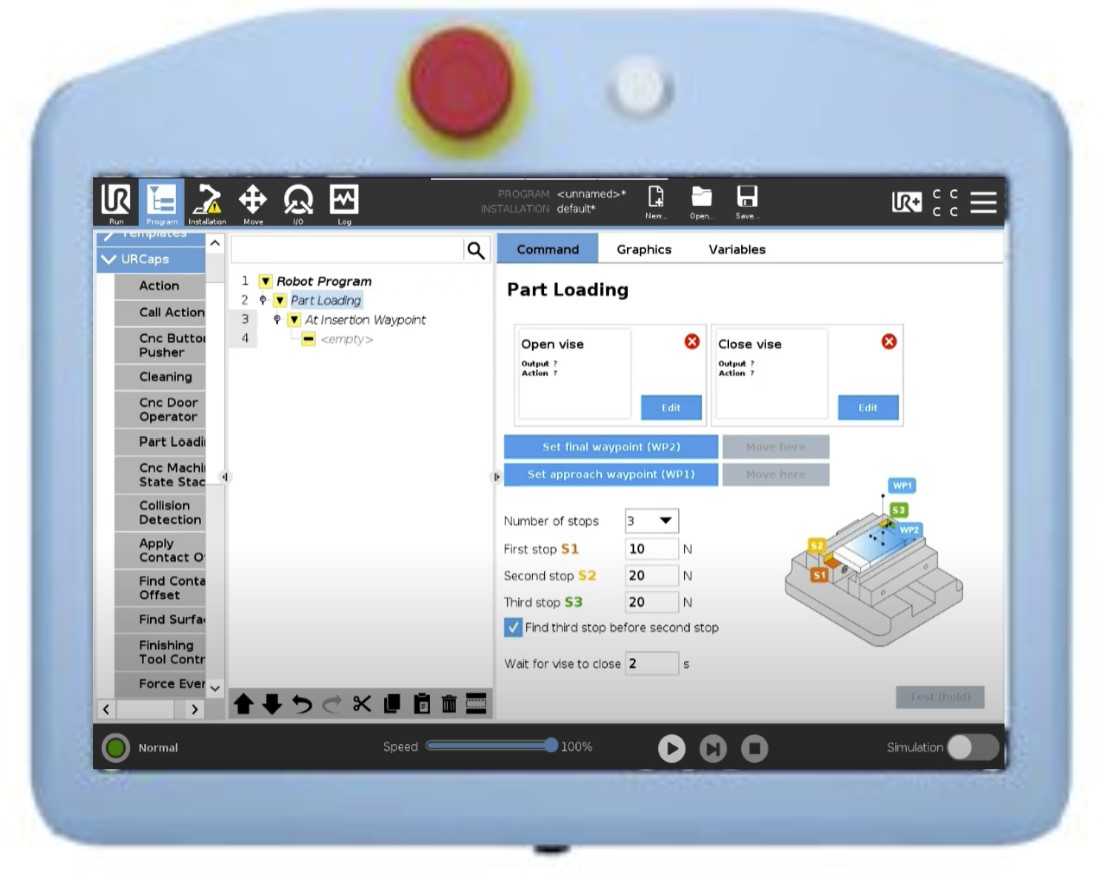
Robotiq software simplifies programming by providing visual guidance and offering simple action menus that speak the language of machinists. The solution offers pre-engineered configurations and automatically optimizes robot trajectories between waypoints, finding the quickest path and avoiding collisions.
Process
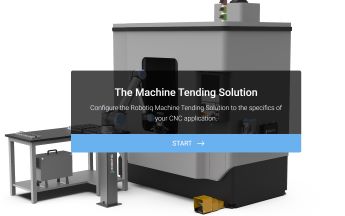
Standardized design for universal compatibility
The Robotiq Machine Tending Solution is designed to work with every CNC machine. Our intuitive fit tool allows for rapid configuration, ensuring a perfect match for specific needs.
Simplifies CNC automation with seamless integration
Integration with Robotiq requires no custom programming or permanent modifications to the CNC control panel, which significantly shortens deployment time.
Copilot software streamlines programming, creating templates tailored to CNC machine types 75% faster. The Program Generator feature automates task-list creation, reducing the need for users to understand program logic.
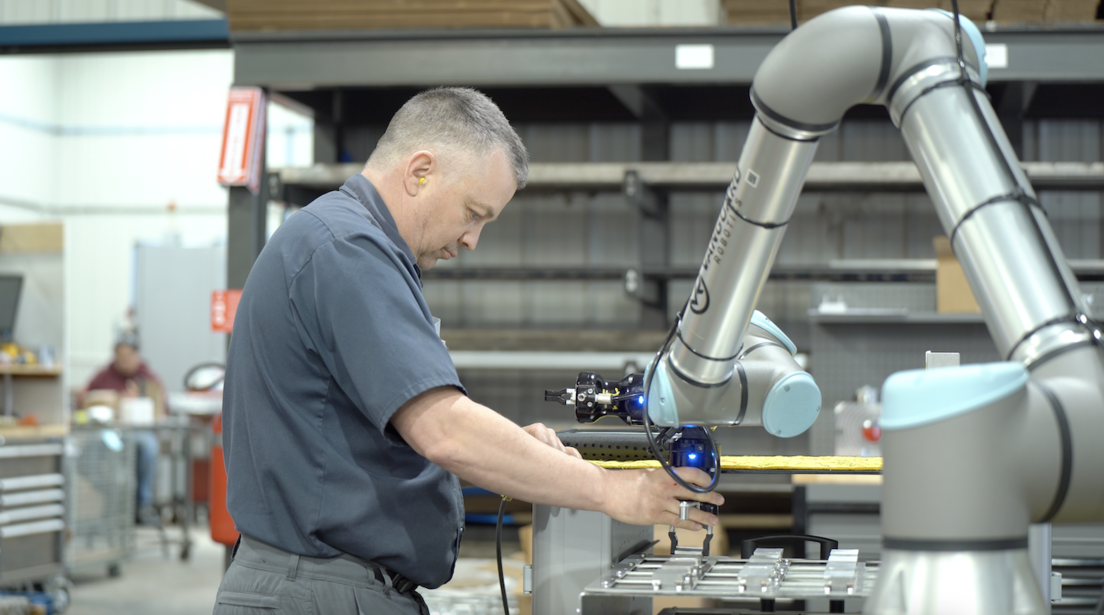
Maximizes uptime and adaptability for efficient CNC operations
The solution’s Copilot software features assistant tools that group configurations and guide users step-by-step, with visual images to aid understanding and foster employee expertise and independence.
External communication modules ensure the solution's adaptability, allowing a smooth transition between automated and manual part feeding, especially for small quantities.
Case Studies
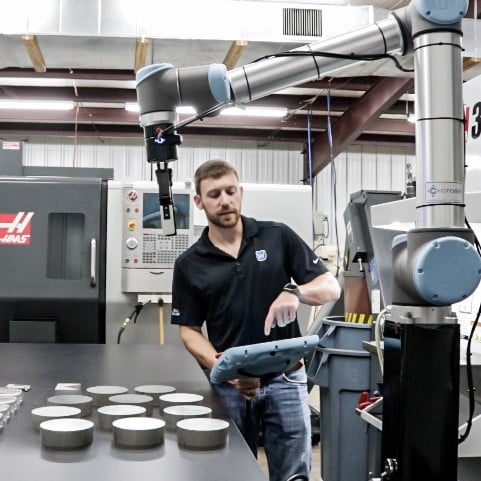
Boost productivity in CNC operations
The Robotiq Machine Tending Solution increases CNC uptime by up to 30%, enhancing overall equipment effectiveness (OEE) in environments where staffing overtime shifts impact profits. It enables one operator to manage quality control for multiple cobots, freeing staff for higher-value tasks and boosting overall labor effectiveness (OLE), which significantly increases efficiency.
Find out how Walt Machine went from making 1,000 parts at a time to 45,000 of these parts.
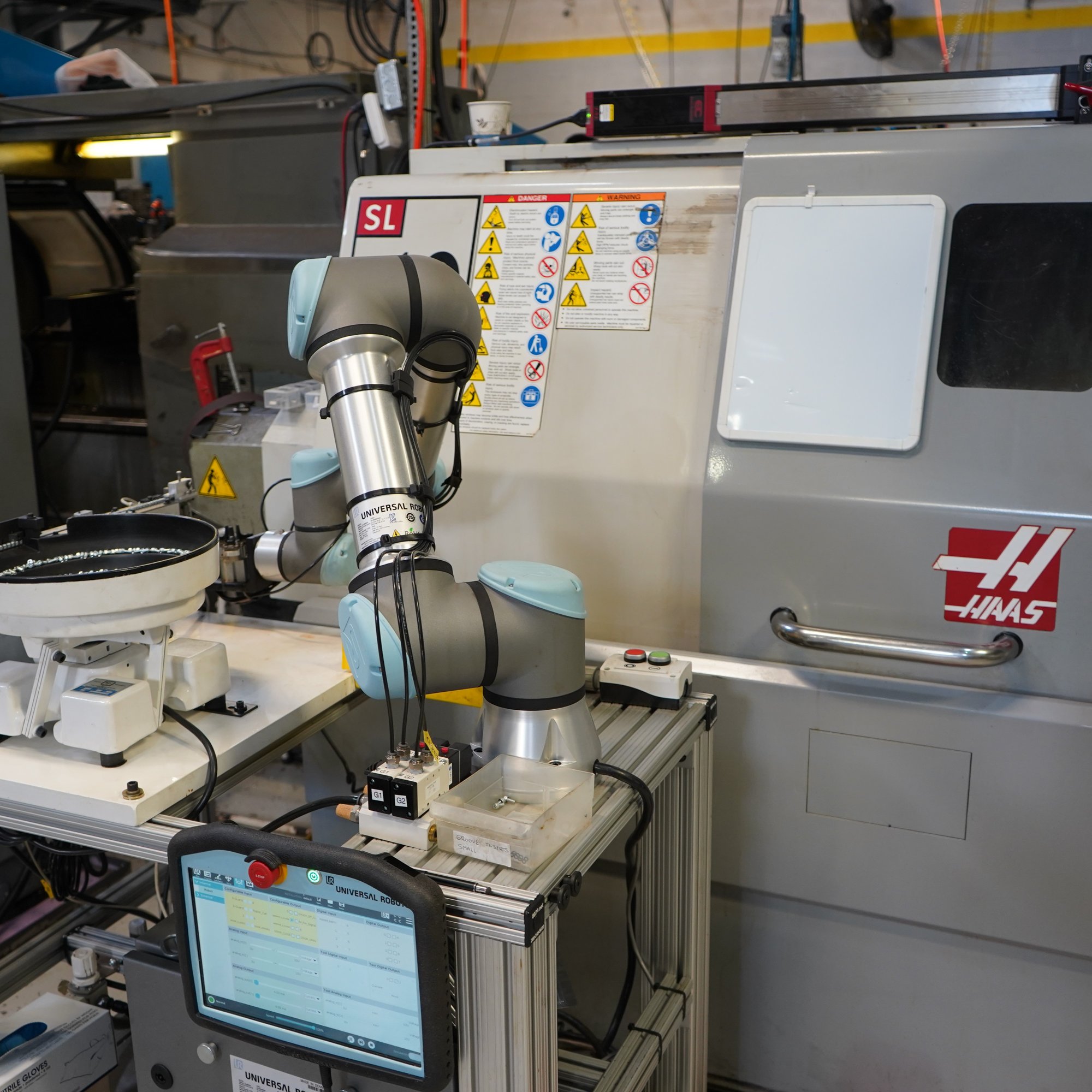
Get flexible automation for sustainable productivity
The Robotiq Machine Tending Solution is versatile and compatible with any CNC model, bypassing costly wiring and custom programming. It maximizes CNC usage and typically delivers a rapid ROI within a year, marking it as a sustainable, profit-enhancing investment.
Learn how one manufacturer, Zago, used the Robotiq Machine Tending Solution to adapt to its many clients' demands.
-3.jpg?width=1612&height=1612&name=Vincent%2BHugo%203%20(3)-3.jpg)
Empower workers amidst labor and market challenges
Manufacturers face the challenges of boosting productivity amid a severe labor shortage, and adapting to ever-evolving market demands. The ongoing struggle to find and retain skilled operators limits CNC machine output and confines staff to unengaging, repetitive tasks, preventing them from realizing their full potential.
Discover how the Robotiq Machine Tending Solution helped Usinatech deal with labor issues.