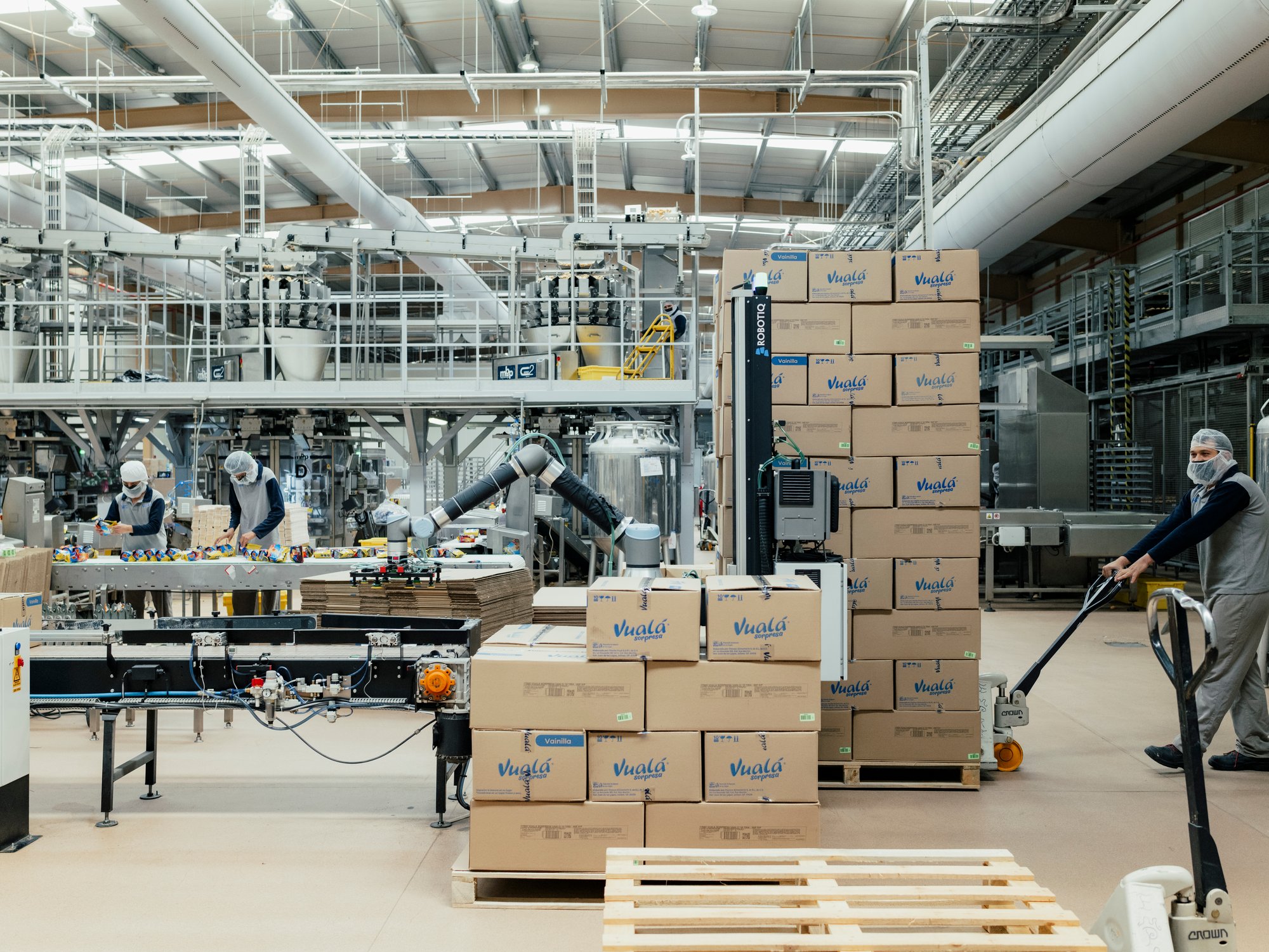
Case Studies
Panovo
Bakery manufacturer Panovo automates palletizing to improve efficiency and operator well-being with 5 Robotiq Solutions
High Pallets
2.5 m (98 in) Stack Height
Repeat Success
5 automated lines with more coming!
Low Temperature
Frozen Baked Goods
Company Overview
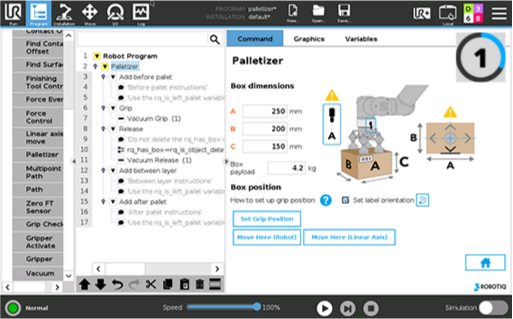
Step 1 - Box dimensions, weight and orientation
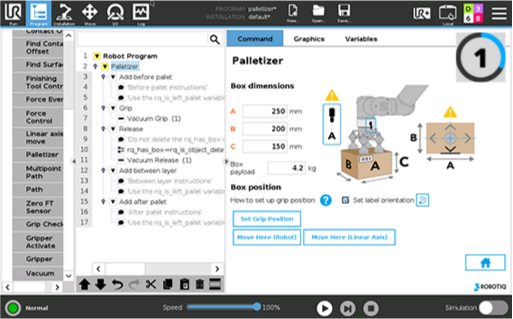
Step 1 - Box dimensions, weight and orientation
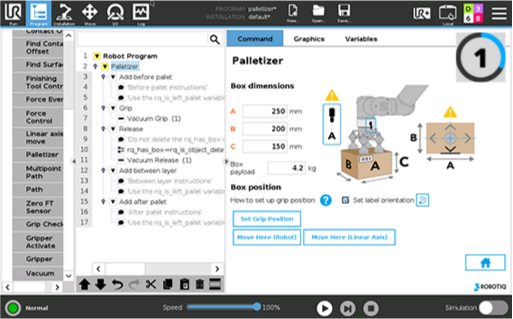
Step 1 - Box dimensions, weight and orientation
About Panovo
Panovo, part of Grupo Proan—the world’s second-largest egg producer—runs nonstop, three shifts a day, seven days a week. With 1,000 employees and a portfolio that includes Vualá snack cakes and frozen baked goods. Panovo is serious about two things: automation and taking care of its people.
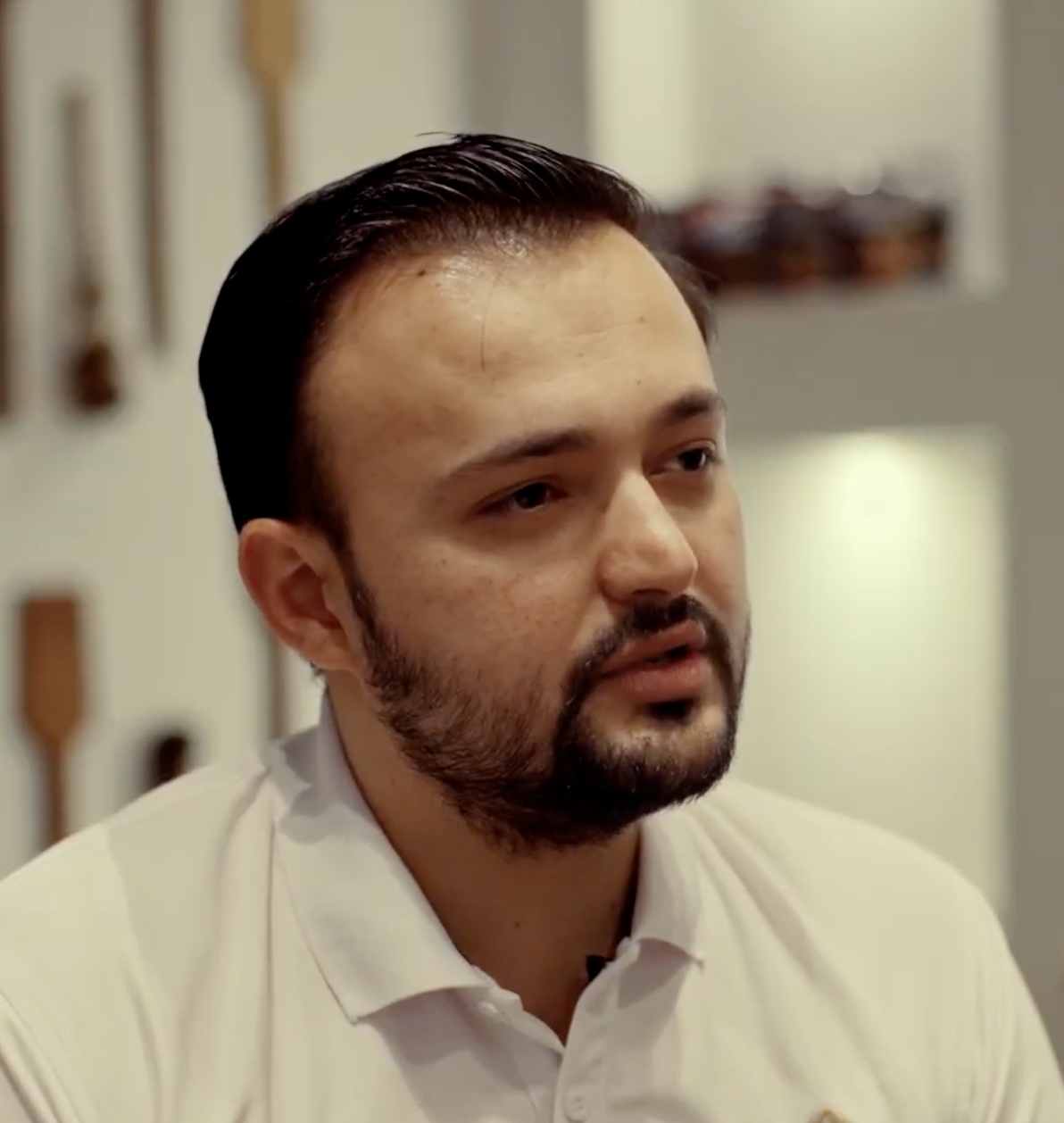
The Problem
- High physical strain and fatigue among operators, especially during night shifts.
- High turnover due to repetitive and physically demanding tasks.
- Ergonomic limitations, particularly due to the 2.5-meter (8.2-foot) pallet height, which made it difficult for operators to safely stack boxes.
- Inconsistent pallet quality, caused by manual stacking errors that impacted logistics and transport.
- Need for space-efficient solutions, as the existing facilities had limited room for large machines.
The Solution
Panovo partnered with Robotiq and HTL to implement collaborative robotic palletizing cells across both their snack and frozen bakery lines.
- 5 Robotiq AX10 Palletizing Solution handling different product formats and reaching up to 2,750 mm (108 in) in stack height.
- Consistent and standardized pallet formation, improving logistics efficiency.
- Solutions implemented in low-temperature environments without issues.
- User-friendly interface, enabling operators to quickly learn and interact with the robots—"as easy as using a smartphone."
- Fast and supportive training from the Robotiq and HTL technical teams.
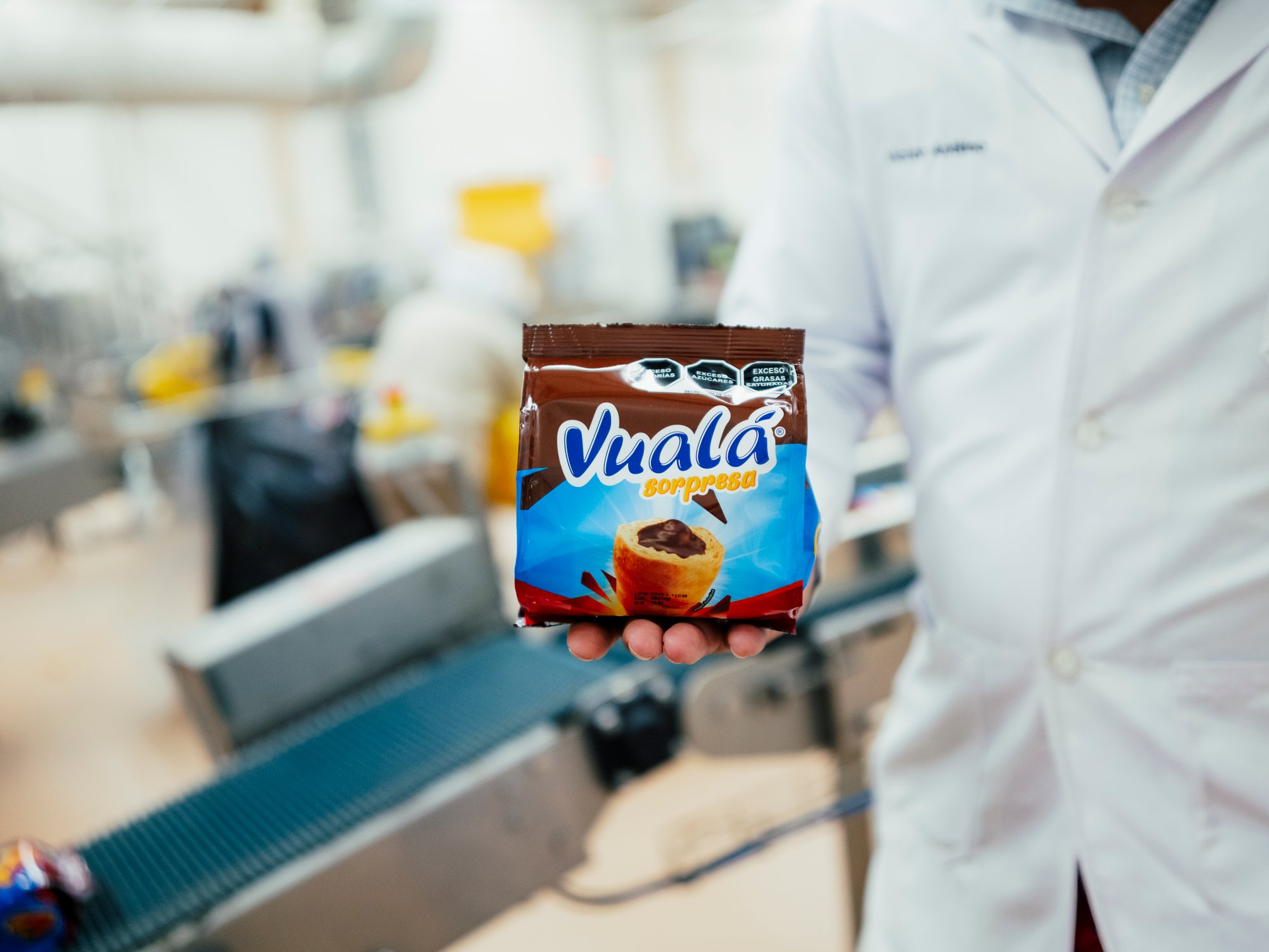
Convincing wins with the Robotiq Palletizing Solution
With plans to expand up to 10 palletizing cells, Panovo’s automation journey is just getting started. The early wins are already prompting the team to explore automation in other parts of the facility—a sign of strong internal buy-in and long-term vision.
EMPLOYEE WELLBEING
With manual palletizing, ergonomic risks were becoming impossible to ignore. Robotiq’s Palletizing Solution removed that strain entirely, improving both safety and workplace comfort across the board.
Replacing repetitive, physically demanding tasks with automation didn’t just reduce injuries—it changed how workers saw their jobs. Instead of resistance, Panovo saw curiosity and enthusiasm. Operators embraced the new technology, leading to higher retention and improved job satisfaction.
OPERATIONAL EFFICIENCY
Beyond the people benefits, Robotiq’s palletizer delivered on the plant’s core goals: reliable, consistent pallet building that improved transport and logistics. The system’s flexibility to handle multiple product types and box formats also gives Panovo the confidence to adapt to whatever’s next.
QUICK ROI & DISRUPTION-FREE
All Palletizing Solutions were selected with a clear benchmark in mind: payback in under 3 years. With faster ramp-ups and minimal disruption, Robotiq made it easy for Panovo to invest in efficiency without slowing down production.
The Robotiq solution
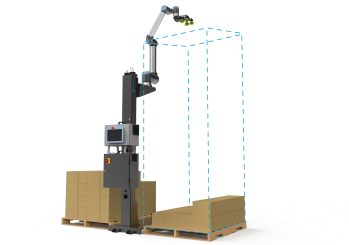
Palletizing
By integrating Robotiq’s collaborative palletizing solutions, Panovo Alimentaria not only tackled labor challenges but also created a safer, more engaging work environment. Their leap into automation—beginning with palletizing—has sparked further innovation across their plants, all while reinforcing their dual commitment to employee wellbeing and operational efficiency.