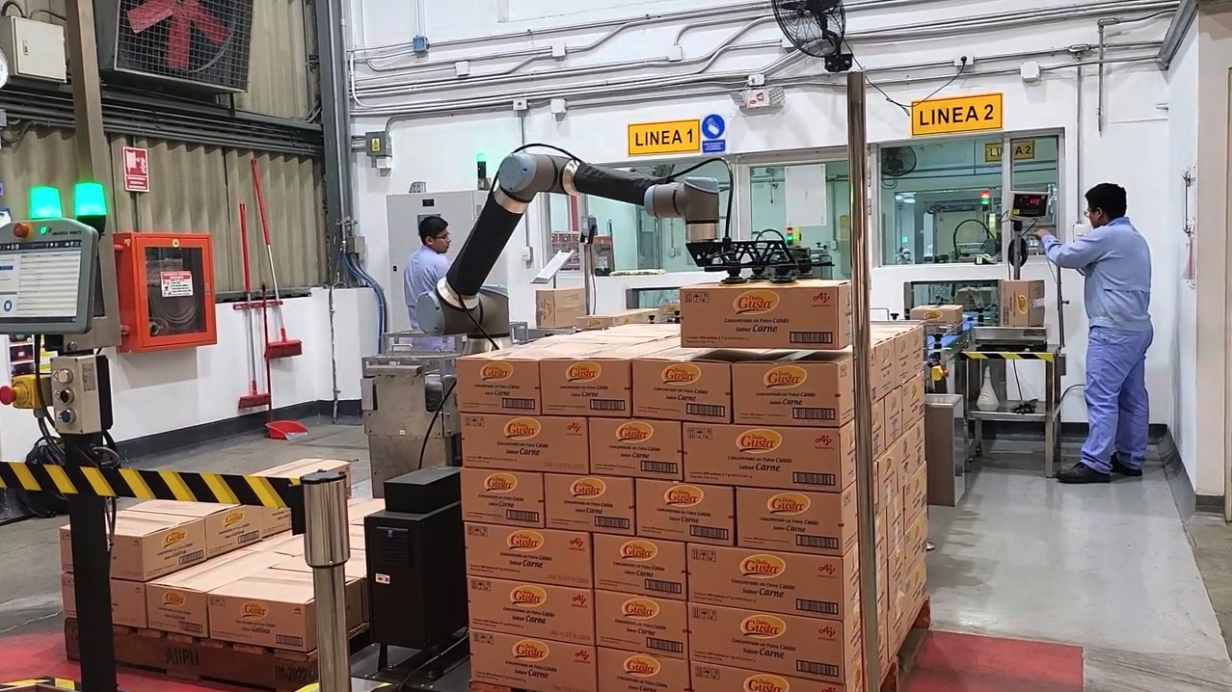
Case Studies
Ajinomoto
Global leader Ajinomoto enhances productivity and safety with Robotiq Palletizing Solution.
Two
Palletizing Solutions
One
AX10
One
PE20
About Ajinomoto
Ajinomoto Co. is a Japanese multinational renowned for its significant contributions to food and amino science. Founded in 1909 by Dr. Kikunae Ikeda, who discovered the umami taste of glutamate, Ajinomoto has become a world leader in the production of seasonings, cooking oils, frozen foods and specialty chemicals. The company operates facilities worldwide, embodying its commitment to improving the flavor and nutrition of food products, aptly reflected in its name, which translates as "Essence of Taste".
Company Overview
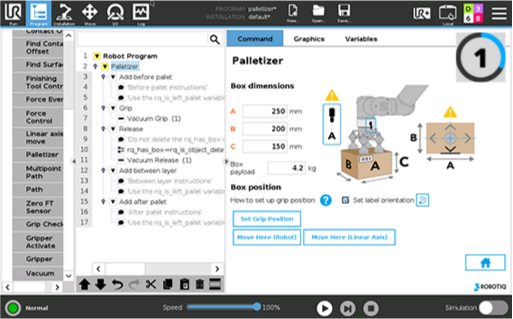
Step 1 - Box dimensions, weight and orientation
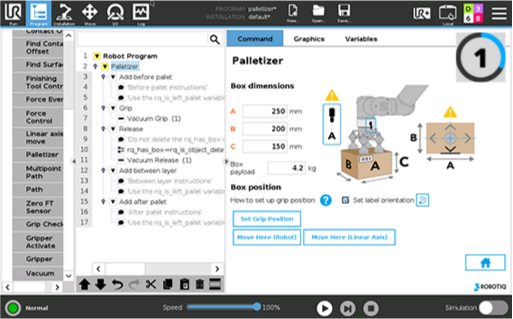
Step 1 - Box dimensions, weight and orientation
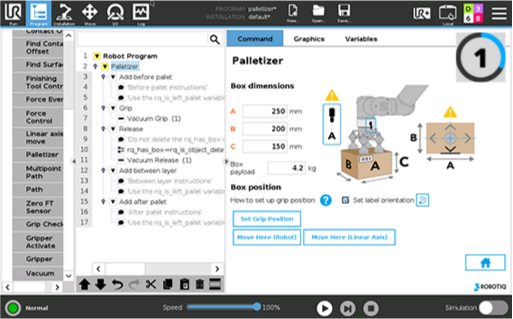
Step 1 - Box dimensions, weight and orientation
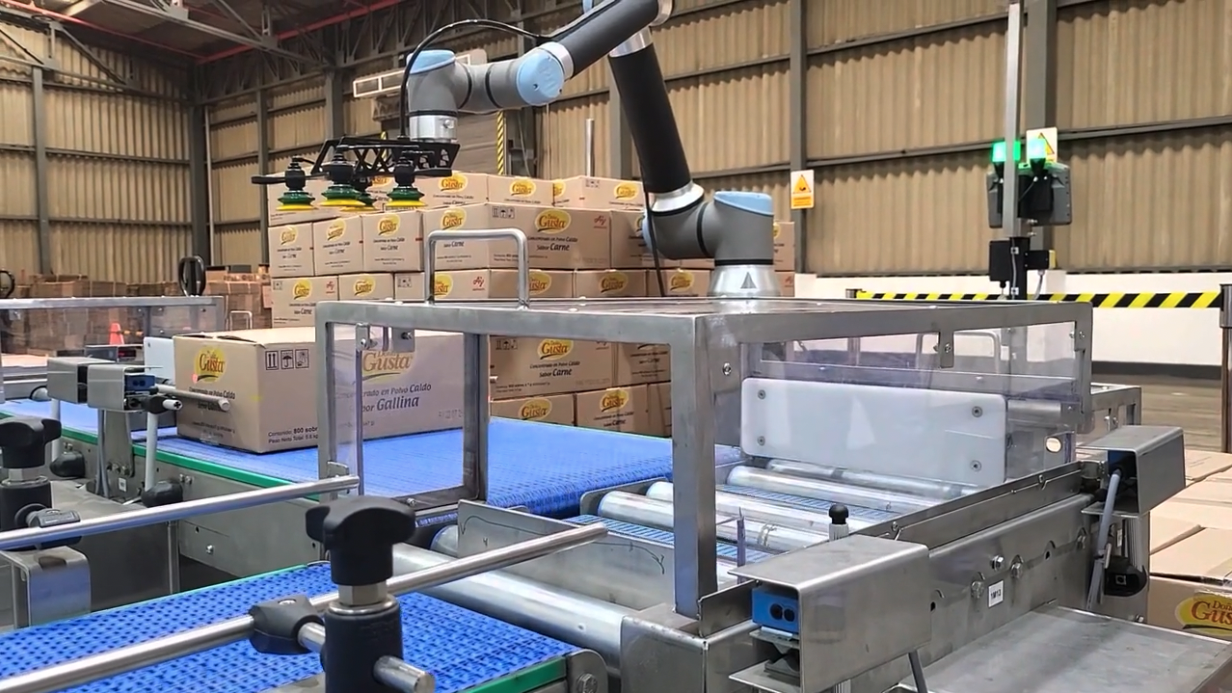
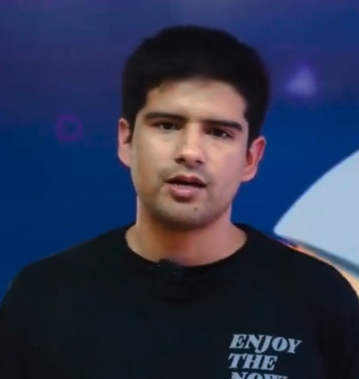
The Problem
At its production site in Peru, Ajinomoto has encountered difficulties in maintaining consistent quality and ergonomic standards on its production lines, particularly for the Doña Augusta product. Production of this particular item relies heavily on manual labor, which not only drives up fixed operating costs, but also introduces considerable safety and product quality risks. These manual, often repetitive and labor-intensive tasks presented potential health risks for employees, and made it difficult to guarantee consistent product quality.
The Solution
To meet these challenges, Ajinomoto integrated Robotiq's AX10 and PE20 Palletizing Solutions into its end-of-line process. This solution was part of a wider initiative to automate key processes with Robotiq's partner IGPS Technologies, and used virtual reality for risk mitigation and training. This strategic integration not only streamlined operations, but also improved the safety and efficiency of Ajinomoto's operations in Peru.
Convincing wins with the Robotiq Palletizing Solution
DIGITAL TRANSFORMATION
The integration of the AX10-PE20 has fostered greater synergy between Ajinomoto's teams. It serves as a cornerstone for the company's digital transformation initiatives, helping to bridge the gap between maintenance, engineering and production teams through improved training and support, facilitated by virtual reality technologies.
ERGONOMIC IMPROVEMENTS
The implementation of the AX10-PE20 has enabled Ajinomoto to significantly reduce fixed costs by automating critical tasks that were previously performed manually. This automation also improved the ergonomics of the production line, reducing physical strain on workers and enhancing workplace safety.
INCREASED PRODUCTIVITY
The automation of the palletizing process has enabled Ajinomoto to achieve a significant increase in productivity. The AX10-PE20 solutions minimize the risk of safety incidents and guarantees consistent quality of packaged products, in line with the company's commitment to excellence and employee well-being.
The Robotiq solution
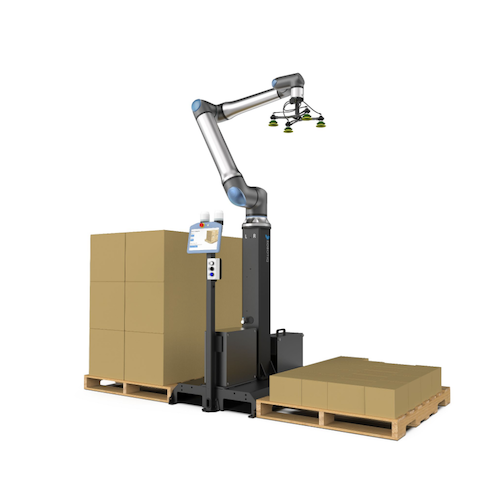
Palletizing
Robotiq's AX10-PE20 collaborative palletizers have revolutionized Ajinomoto's approach to the end-of-line packaging process. By automating the stacking and organization of products on pallets, this system has streamlined operations, enabling faster turnaround times and more efficient use of warehouse space. This strategic implementation is in line with Ajinomoto's objectives of optimizing productivity and guaranteeing the highest standards of quality and safety in its facilities.