The conversation around automation often starts with cost. Factory leaders ask: “Will this...
.gif?width=1152&height=648&name=Untitled%20design%20(52).gif)
Robotiq Palletizing Solutions
Simple to deploy. Proven to perform. Built to scale.
Automation made easy — really.
Manual palletizing is hard to staff and harder to scale. Our solution changes that.
The Robotiq Palletizing Solution is fast to set up, easy to use, and ready to scale with your business.
It’s everything you need, nothing you don’t.
Presentation
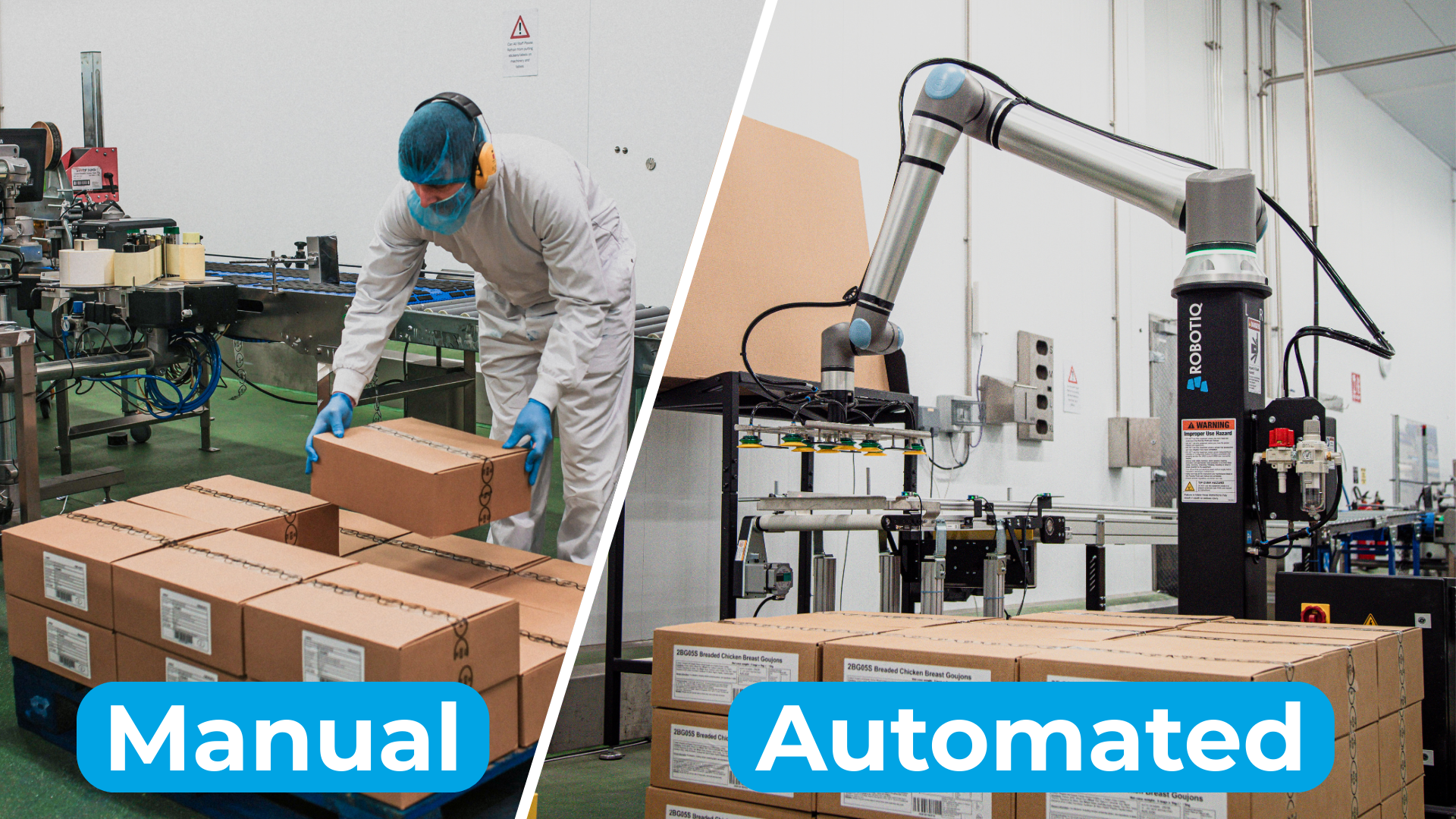
Robotiq Palletizing Solution - small steps, big impact
Your end-of-line is the final stop before delivery to your customers. It's also one of the most manual and labor-intensive.
Robotiq helps you automate it—without complexity, long timelines, or rigid systems.
Empower your people. Boost your factory productivity. Enhance your adaptability.
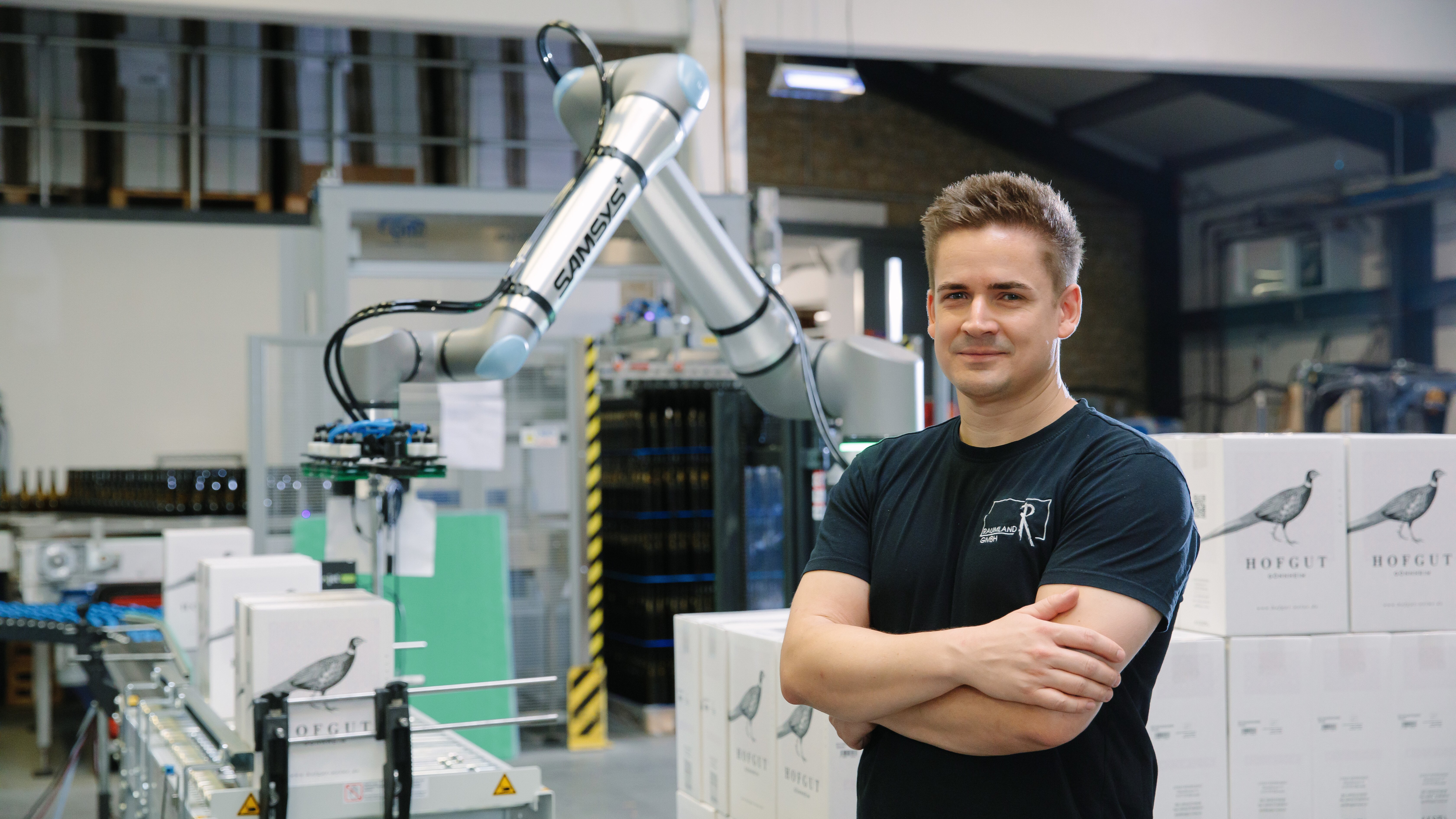
Empower people
Remove repetitive tasks and reduce strain.
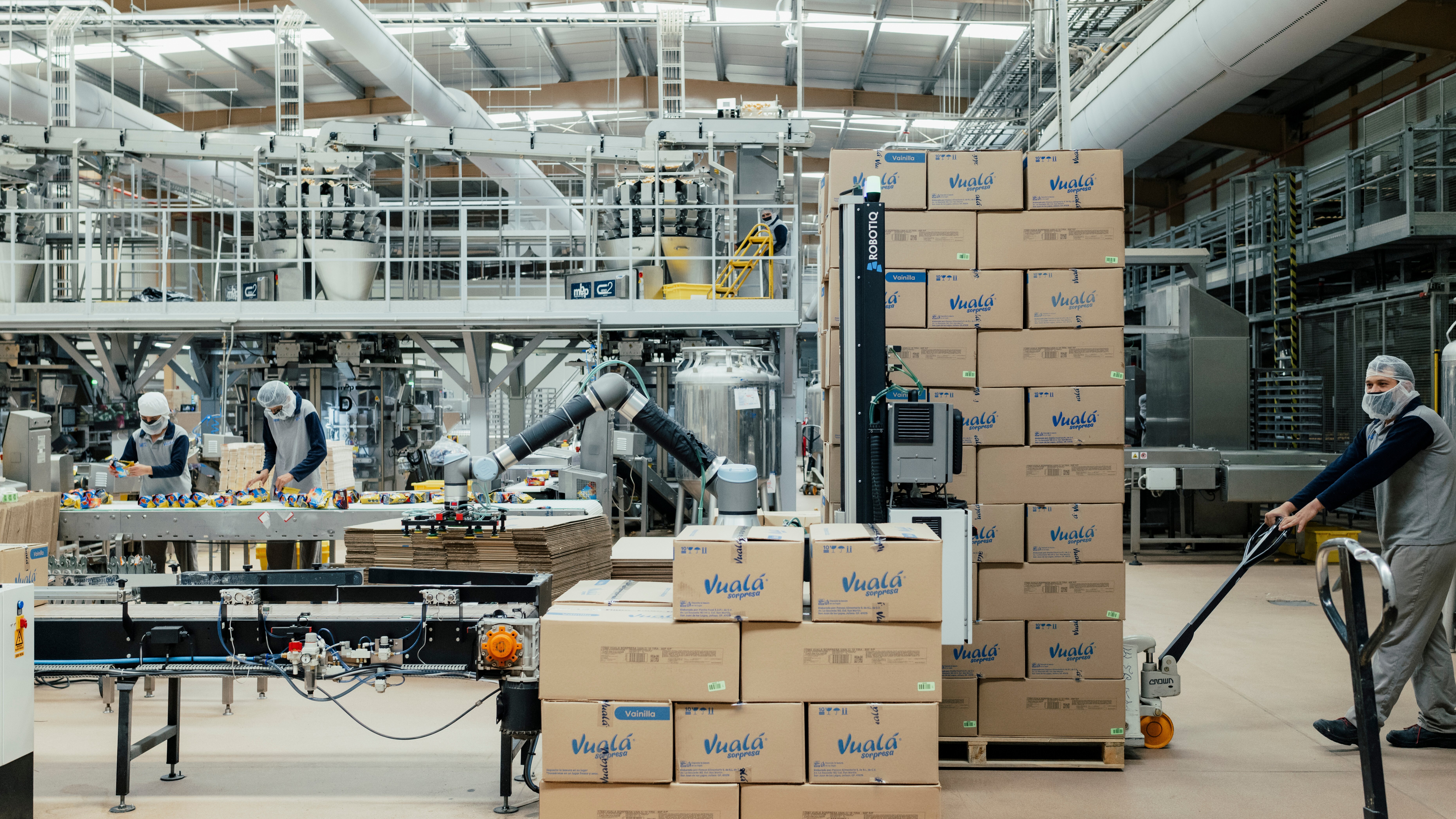
Boost productivity
Easy to set up. Easy to use. No robotics experience needed.
Predictable payback in 1-2 years.
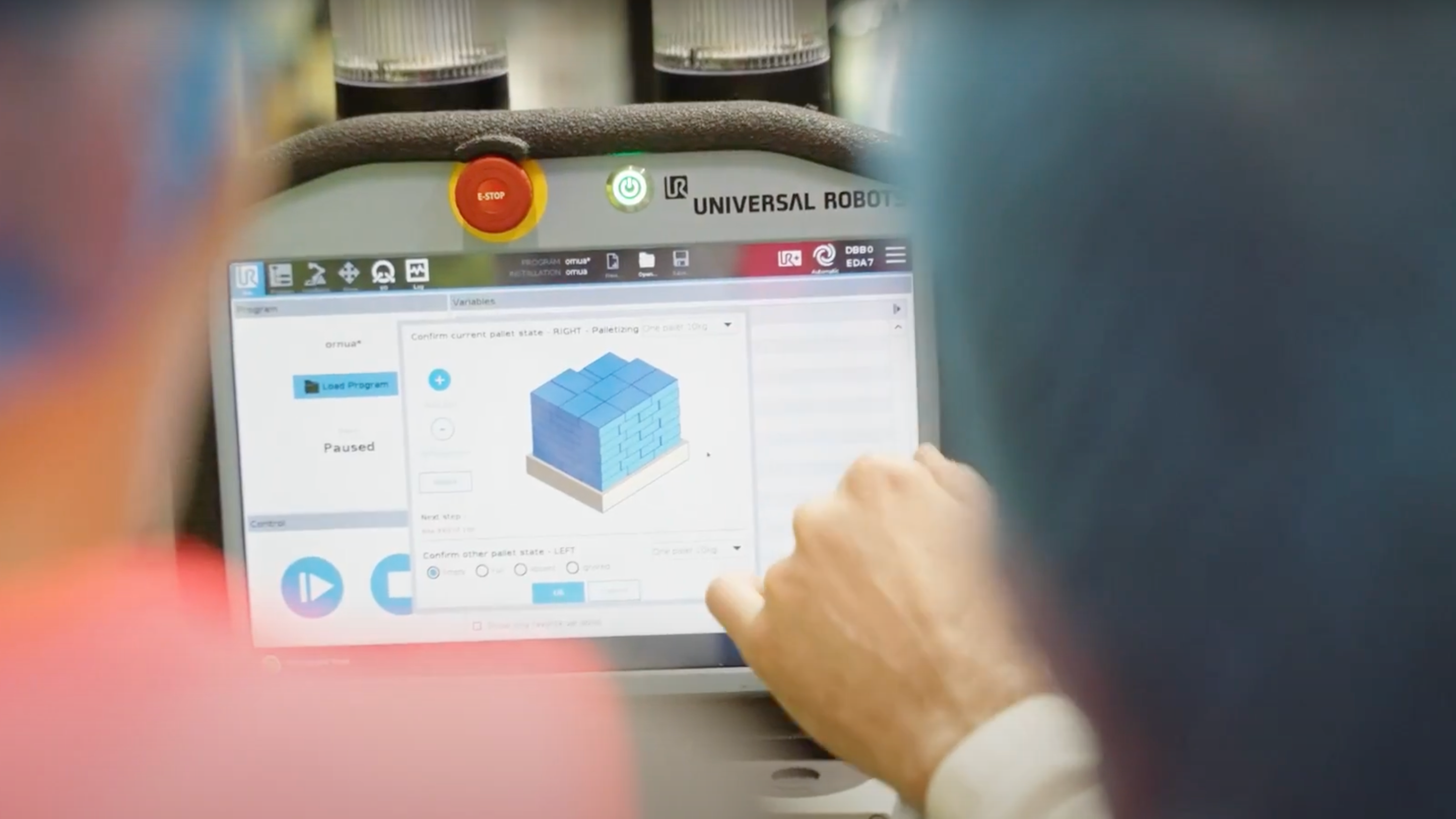
Enhance adaptability
Handle new SKUs, pallet patterns, and setups with ease.
Structured decision-making process with practical tools to assist you in making a smart choice.
What's included in the Robotiq Palletizing Solution?
Complete lineup of Robotiq Palletizing Solutions
Choose the right fit for your factory.
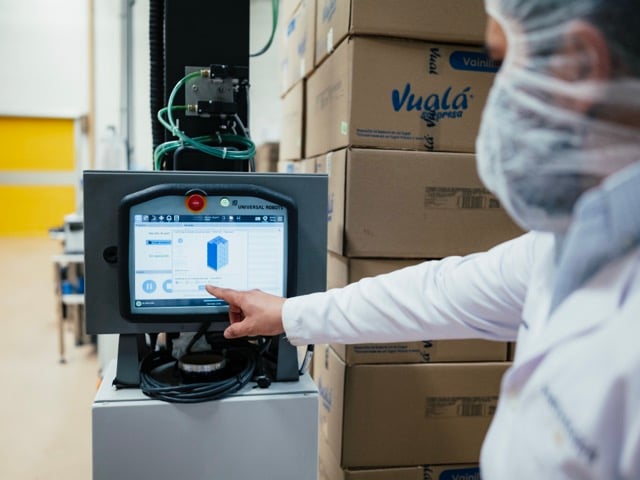
CoPilot palletizing software that works like your best operator
- Visual setup requires no code
- Auto-optimizes trajectories
- Handles obstacles and tight layouts
- Allows for cloning and reusing recipes
- Built-in Force & Torque sensor for stacking precision
A complete, proven system—delivered turnkey.
When you choose Robtoiq, you're not just getting a palletizer—you’re getting end-to-end support, from initial design to full-scale operation:
- Turnkey setup in 3 days
- Training included
- Backed by Lean Robotics methodology
- Delivered by certified Expert Partners or by Robotiq Installation Services
-
6500
Cases palletized in a day
6500
Cases palletized in a day
6500
Cases palletized in a day
Applications
Versatile Applications of Hand-E Grippers by Robotiq
Quality Testing
Read more
Quality Testing
Read more
Quality Testing
Read more
Quality Testing
Read more
Features
Key Features of Hand-E Gripper by Robotiq
Built for collaborative robots
- 50-mm stroke gripper model is suited to collaborative robots
- Integrates seamlessly with Robotiq’s Wrist Camera and FT 300 Force Torque Sensor
- Ergonomic shape for hand-guiding
Built for collaborative robots
- 50-mm stroke gripper model is suited to collaborative robots
- Integrates seamlessly with Robotiq’s Wrist Camera and FT 300 Force Torque Sensor
- Ergonomic shape for hand-guiding
Built for collaborative robots
- 50-mm stroke gripper model is suited to collaborative robots
- Integrates seamlessly with Robotiq’s Wrist Camera and FT 300 Force Torque Sensor
- Ergonomic shape for hand-guiding
Built for collaborative robots
- 50-mm stroke gripper model is suited to collaborative robots
- Integrates seamlessly with Robotiq’s Wrist Camera and FT 300 Force Torque Sensor
- Ergonomic shape for hand-guiding
Integration
Easy to integrate, easy to use
Robotiq’s Hand-E Gripper is simple to integrate in your production environment and easy for workers of all skill levels to use—no robotics experience required.Install your adaptive gripper in just a few minutes, thanks to our Plug + Play gripper kits. Then use our intuitive software interface to program directly on your robot’s touchscreen.
Accelerate your production line
Increase productivity and improve your cycle time with a dual configuration, which lets you handle more objects at a time. The dual Hand-E configuration is the perfect way to keep your CNC machine fed, even when your operators are away.
Accelerate your production line
Increase productivity and improve your cycle time with a dual configuration, which lets you handle more objects at a time. The dual Hand-E configuration is the perfect way to keep your CNC machine fed, even when your operators are away.
Accelerate your production line
Increase productivity and improve your cycle time with a dual configuration, which lets you handle more objects at a time. The dual Hand-E configuration is the perfect way to keep your CNC machine fed, even when your operators are away.
Technical Documentation
Gorem ipsum dolor sit amet, consectetur adipiscing elit.
Robotiq has a variety of technical information available for your solution.
Every product launch has a first. For the Robotiq AX30, that moment came when one of the world’s...
Specifications
Morem ipsum dolor sit amet
Qorem ipsum dolor sit amet, consectetur adipiscing elit. Nunc vulputate libero et velit interdum, ac aliquet odio mattis.
Stroke 50 mm (2.0 in) Stroke 50 mm (2.0 in) Stroke 50 mm (2.0 in) Stroke 50 mm (2.0 in) Stroke 50 mm (2.0 in) Stroke 50 mm (2.0 in) Stroke 50 mm (2.0 in) *Calculated for the use of silicon covered fingertips to grip a steel object, at a low robot acceleration.
Customers stories
Gorem ipsum dolor sit amet, consectetur adipiscing elit.
See how the 2-Finger Adaptive Robot Gripper helped triple Voodoo Manufacturing's 3D printing production
The ROI was a slam dunk from the beginning, from how much labor it saved. The installation process was the smoothest install of any piece of equipment I have had to experience in 28 years.
Greg Thayer
Vice-President, Cascade
coffee
Vacuum Grippers
The PowerPick vacuum gripper line is designed to handle a wide range of applications, with a key focus on maximizing lifting capacity, productivity, and adaptability, making the grippers preferred choices to perform heavy-duty tasks like palletizing.
PowerPick Multi elevates your palletizing solution by eliminating gripper changeovers and manual handling. Its flexible cup array, dual-zone picking, and intuitive URCap integration make it easy to adapt to any box size and future production changes.
Equipped with a vacuum generator that attaches to the base of the robot, the PowerPick 10-20-30 set a new standard for lightweight and enhanced lifting performance in their category.
Learn more about our Vacuum Grippers. -
6500
Cases palletized in a day
6500
Cases palletized in a day
6500
Cases palletized in a day
Applications
Versatile Applications of Hand-E Grippers by Robotiq
Quality Testing
Read more
Quality Testing
Read more
Quality Testing
Read more
Quality Testing
Read more
Features
Key Features of Hand-E Gripper by Robotiq
Built for collaborative robots
- 50-mm stroke gripper model is suited to collaborative robots
- Integrates seamlessly with Robotiq’s Wrist Camera and FT 300 Force Torque Sensor
- Ergonomic shape for hand-guiding
Built for collaborative robots
- 50-mm stroke gripper model is suited to collaborative robots
- Integrates seamlessly with Robotiq’s Wrist Camera and FT 300 Force Torque Sensor
- Ergonomic shape for hand-guiding
Built for collaborative robots
- 50-mm stroke gripper model is suited to collaborative robots
- Integrates seamlessly with Robotiq’s Wrist Camera and FT 300 Force Torque Sensor
- Ergonomic shape for hand-guiding
Built for collaborative robots
- 50-mm stroke gripper model is suited to collaborative robots
- Integrates seamlessly with Robotiq’s Wrist Camera and FT 300 Force Torque Sensor
- Ergonomic shape for hand-guiding
Integration
Easy to integrate, easy to use
Robotiq’s Hand-E Gripper is simple to integrate in your production environment and easy for workers of all skill levels to use—no robotics experience required.Install your adaptive gripper in just a few minutes, thanks to our Plug + Play gripper kits. Then use our intuitive software interface to program directly on your robot’s touchscreen.
Accelerate your production line
Increase productivity and improve your cycle time with a dual configuration, which lets you handle more objects at a time. The dual Hand-E configuration is the perfect way to keep your CNC machine fed, even when your operators are away.
Accelerate your production line
Increase productivity and improve your cycle time with a dual configuration, which lets you handle more objects at a time. The dual Hand-E configuration is the perfect way to keep your CNC machine fed, even when your operators are away.
Accelerate your production line
Increase productivity and improve your cycle time with a dual configuration, which lets you handle more objects at a time. The dual Hand-E configuration is the perfect way to keep your CNC machine fed, even when your operators are away.
Technical Documentation
Gorem ipsum dolor sit amet, consectetur adipiscing elit.
Robotiq has a variety of technical information available for your solution.
Every product launch has a first. For the Robotiq AX30, that moment came when one of the world’s...
Specifications
Morem ipsum dolor sit amet
Qorem ipsum dolor sit amet, consectetur adipiscing elit. Nunc vulputate libero et velit interdum, ac aliquet odio mattis.
Stroke 50 mm (2.0 in) Stroke 50 mm (2.0 in) Stroke 50 mm (2.0 in) Stroke 50 mm (2.0 in) Stroke 50 mm (2.0 in) Stroke 50 mm (2.0 in) Stroke 50 mm (2.0 in) *Calculated for the use of silicon covered fingertips to grip a steel object, at a low robot acceleration.
Customers stories
Gorem ipsum dolor sit amet, consectetur adipiscing elit.
See how the 2-Finger Adaptive Robot Gripper helped triple Voodoo Manufacturing's 3D printing production
The ROI was a slam dunk from the beginning, from how much labor it saved. The installation process was the smoothest install of any piece of equipment I have had to experience in 28 years.
Greg Thayer
Vice-President, Cascade
coffee
Safety Packages
Maximize performance with confidence while keeping a safe environment and a small footprint.
Safety packages are a modular and easy-to-integrate add-on designed to ensure palletizer cell safe operation for scenarios with high payload, stack height, cobot speed & throughput and any other threshold identified by the risk assessment.
✅ Keep your palletizing cell open
Avoid bulky fences during pallet change
✅ Maximize factory space
Keep a small footprint
✅ Maximize performance safely
Get the most out of your palletizing
solution while keeping a safe environment -
6500
Cases palletized in a day
6500
Cases palletized in a day
6500
Cases palletized in a day
Applications
Versatile Applications of Hand-E Grippers by Robotiq
Quality Testing
Read more
Quality Testing
Read more
Quality Testing
Read more
Quality Testing
Read more
Features
Key Features of Hand-E Gripper by Robotiq
Built for collaborative robots
- 50-mm stroke gripper model is suited to collaborative robots
- Integrates seamlessly with Robotiq’s Wrist Camera and FT 300 Force Torque Sensor
- Ergonomic shape for hand-guiding
Built for collaborative robots
- 50-mm stroke gripper model is suited to collaborative robots
- Integrates seamlessly with Robotiq’s Wrist Camera and FT 300 Force Torque Sensor
- Ergonomic shape for hand-guiding
Built for collaborative robots
- 50-mm stroke gripper model is suited to collaborative robots
- Integrates seamlessly with Robotiq’s Wrist Camera and FT 300 Force Torque Sensor
- Ergonomic shape for hand-guiding
Built for collaborative robots
- 50-mm stroke gripper model is suited to collaborative robots
- Integrates seamlessly with Robotiq’s Wrist Camera and FT 300 Force Torque Sensor
- Ergonomic shape for hand-guiding
Integration
Easy to integrate, easy to use
Robotiq’s Hand-E Gripper is simple to integrate in your production environment and easy for workers of all skill levels to use—no robotics experience required.Install your adaptive gripper in just a few minutes, thanks to our Plug + Play gripper kits. Then use our intuitive software interface to program directly on your robot’s touchscreen.
Accelerate your production line
Increase productivity and improve your cycle time with a dual configuration, which lets you handle more objects at a time. The dual Hand-E configuration is the perfect way to keep your CNC machine fed, even when your operators are away.
Accelerate your production line
Increase productivity and improve your cycle time with a dual configuration, which lets you handle more objects at a time. The dual Hand-E configuration is the perfect way to keep your CNC machine fed, even when your operators are away.
Accelerate your production line
Increase productivity and improve your cycle time with a dual configuration, which lets you handle more objects at a time. The dual Hand-E configuration is the perfect way to keep your CNC machine fed, even when your operators are away.
Technical Documentation
Gorem ipsum dolor sit amet, consectetur adipiscing elit.
Robotiq has a variety of technical information available for your solution.
Every product launch has a first. For the Robotiq AX30, that moment came when one of the world’s...
Specifications
Morem ipsum dolor sit amet
Qorem ipsum dolor sit amet, consectetur adipiscing elit. Nunc vulputate libero et velit interdum, ac aliquet odio mattis.
Stroke 50 mm (2.0 in) Stroke 50 mm (2.0 in) Stroke 50 mm (2.0 in) Stroke 50 mm (2.0 in) Stroke 50 mm (2.0 in) Stroke 50 mm (2.0 in) Stroke 50 mm (2.0 in) *Calculated for the use of silicon covered fingertips to grip a steel object, at a low robot acceleration.
Customers stories
Gorem ipsum dolor sit amet, consectetur adipiscing elit.
See how the 2-Finger Adaptive Robot Gripper helped triple Voodoo Manufacturing's 3D printing production
The ROI was a slam dunk from the beginning, from how much labor it saved. The installation process was the smoothest install of any piece of equipment I have had to experience in 28 years.
Greg Thayer
Vice-President, Cascade
coffee
Interlayer (Slipsheet) Feeding System
Interlayer Feeding System are designed to streamline the handling of rigid cardboard slipsheets in your automated palletizing workflow.
- Easily adaptable to handle different size interlayers with minimal downtime.
- Provides all necessary programming to seamlessly incorporate interlayer placement into your pallet recipes.
How we make it work for you
How it fits in your factory
Want to see if a Robotiq Palletizing Solution fits your operation? Answer a few questions and we'll show you which setup works best for you. You'll receive:
- A recommendation for the best-fitting Robotiq palletizing model
- An automatically-generated 3D simulation of the Robotiq Palletizing Solution customized to your needs
- A detailed ROI and payback period calculation
- A downloadable report to share internally
Small footprint
Installs in 3 days. Fits your space. Scales with you.
No need to reconfigure your line or halt production.
Robotiq’s compact system fits your layout now and grows with it later.
Come see it in action
Prefer a hands-on look? See a map of local Expert Partners for a live demo—bring your own products and see it in action.
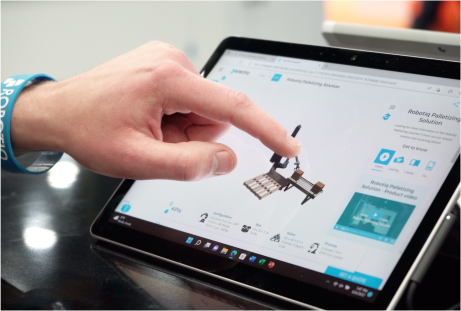
How we get you from idea to operation
Our Application Experts will guide you through the deployment process.
- Design: We gather your information and simulate a fit
- Integrate: Pre-tested, optional FAT (Factory Acceptance Testing)
- Operate: Local install and training in three days
How much does it cost?
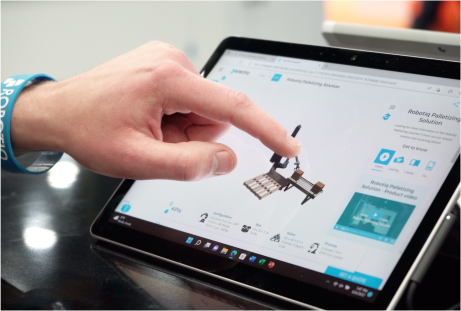
How much does it cost?
The exact cost depends on your factory’s setup, but the payoff is clear—most factories see ROI in 1–2 years through labor savings, higher output, and lower hiring costs.
Want real numbers for your operation? Try our ROI calculator to crunch the numbers.
Ready to move forward?
Who's using it?
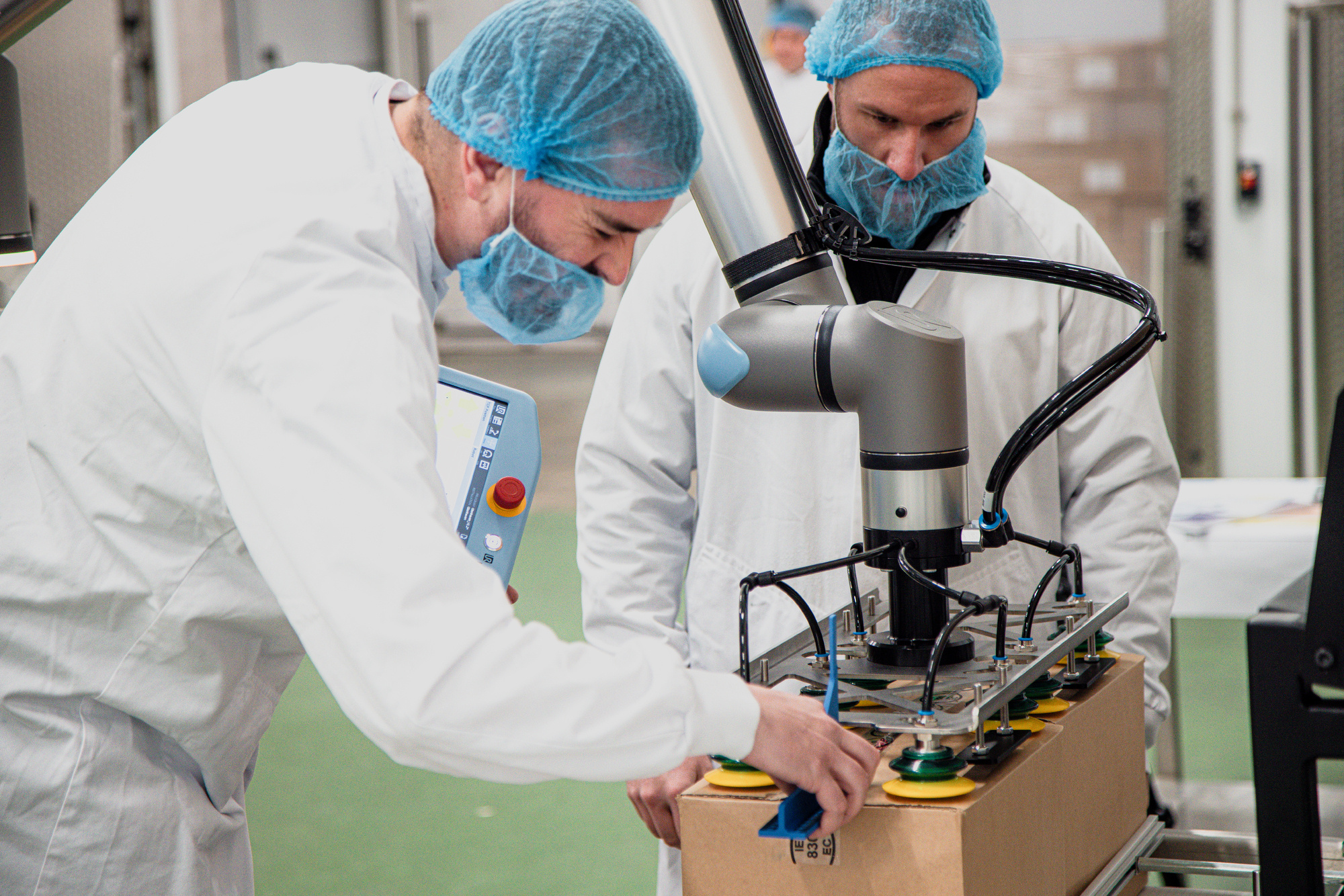
"So really it's a very quick, fast, simple solution, and it's one that can be rolled out at pace across multiple lines within a factory."
- Ken Maguire
Managing Director, Glenhaven Foods
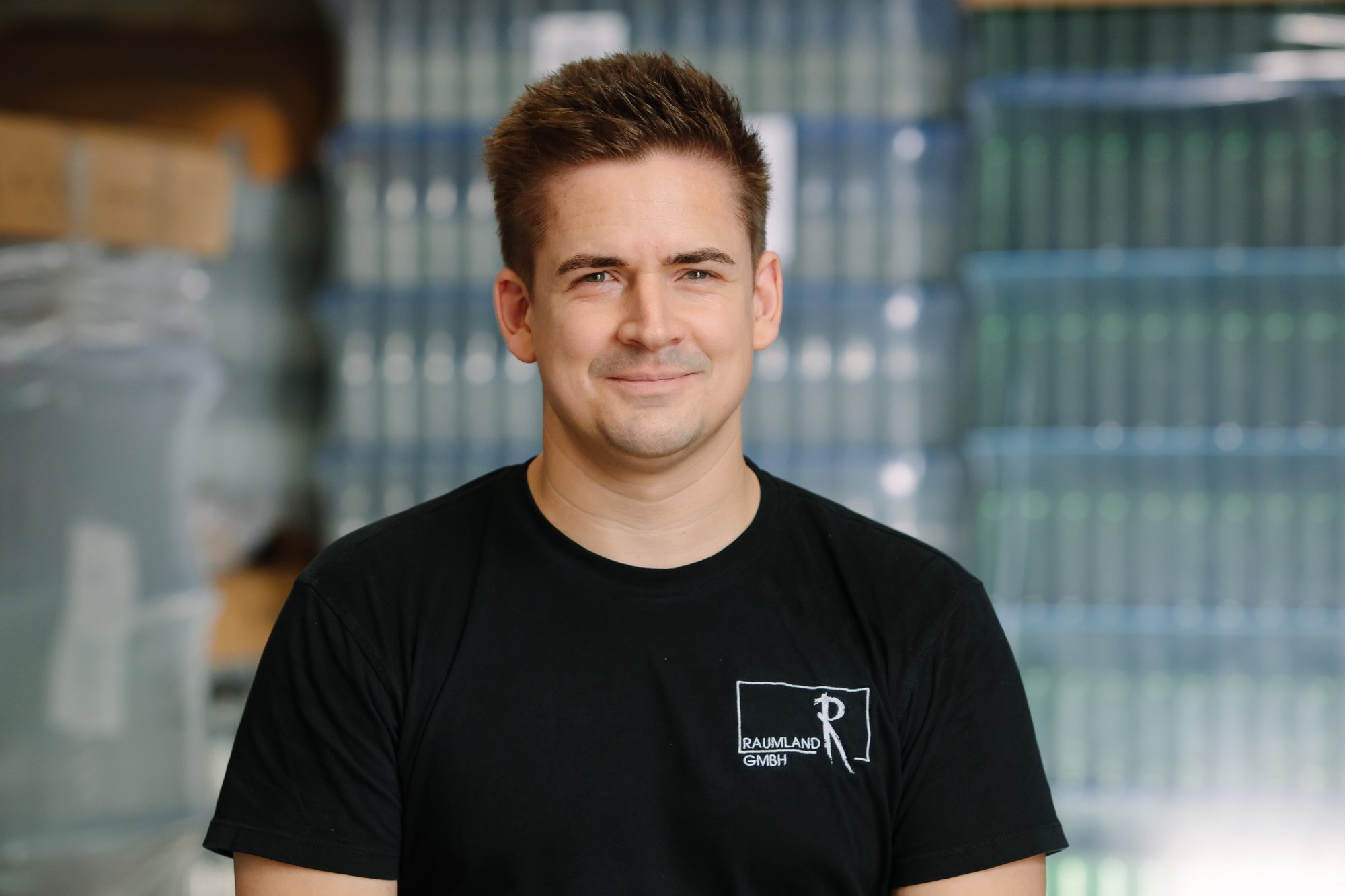
"The cobot perfectly reflects what we need. It is a flexible machine, compact, quick to set up, and, ultimately, affordable. We were able to automate a task that was extremely tedious. No one complains about back pain anymore. At least not from palletizing."
- Sebastian Raumland
Managing Director, Raumland GmbH
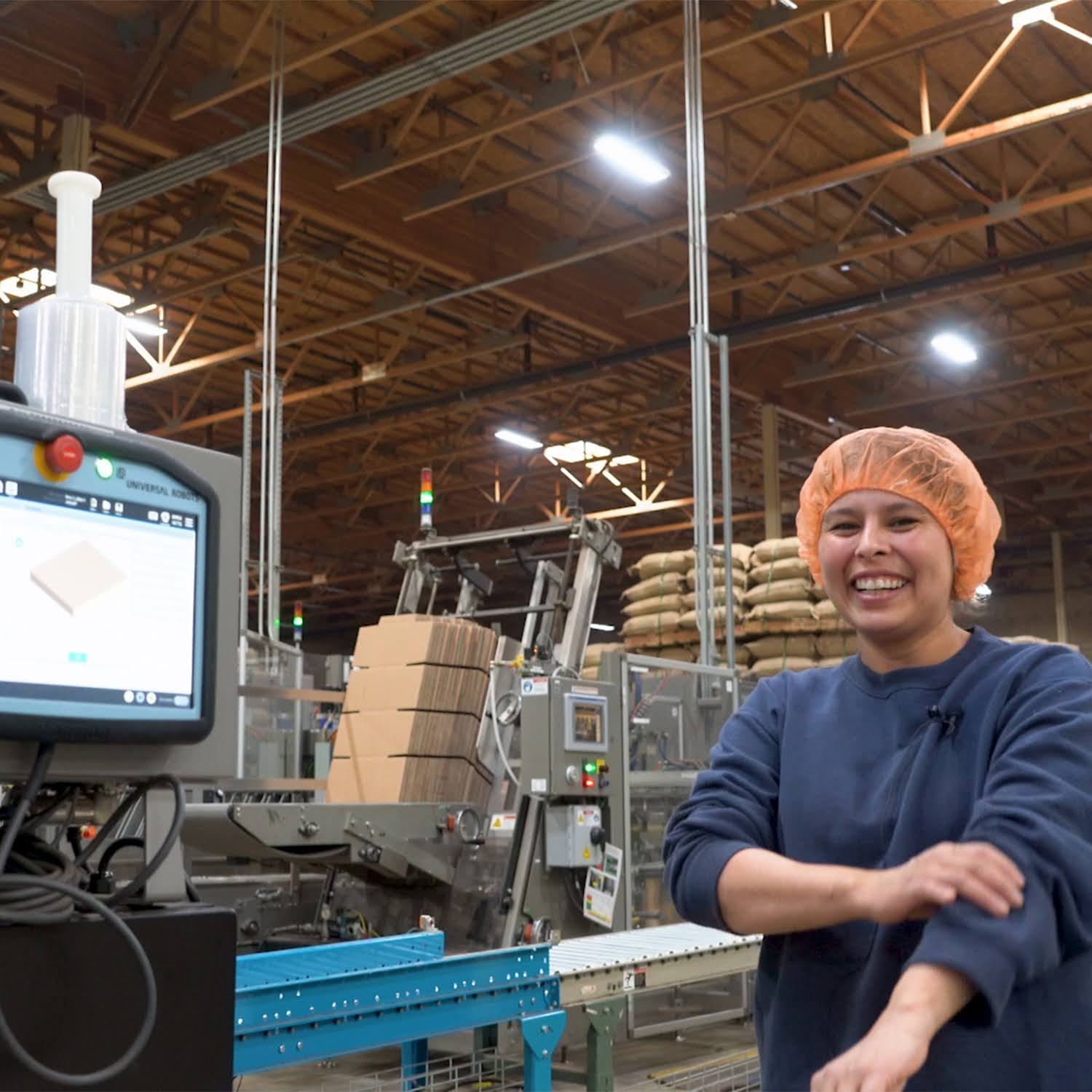
"The ROI was a slam dunk from the beginning, from how much labor it saved. The installation process was the smoothest install of any piece of equipment I have had to experience in 28 years."
- Greg Thayer
Vice-President, Cascade Coffee
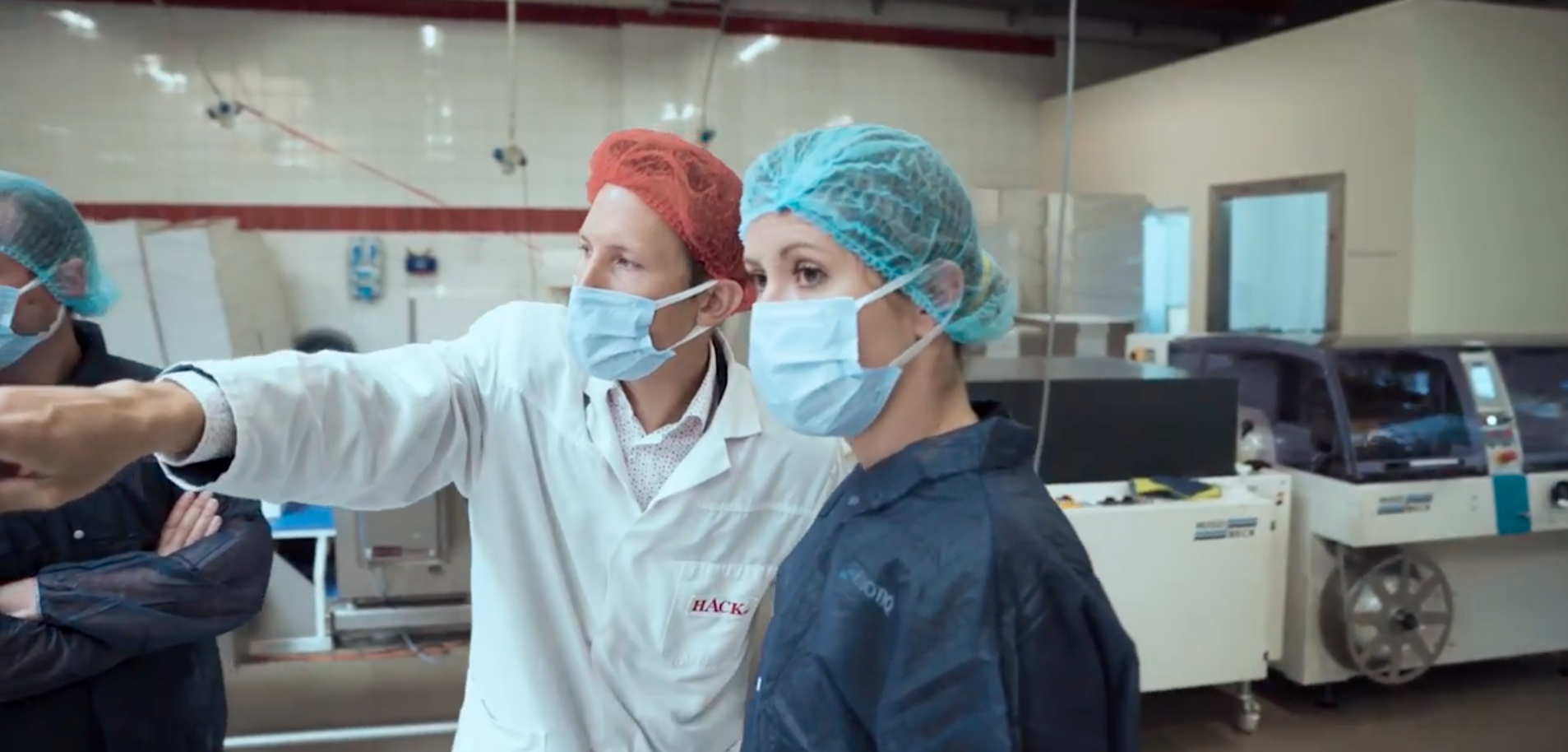
"The key result for our production process is that we are now further flexible in our processes and product planning, and we decreased the hard work of our employees."
- Simon Gunnemann
Managing director central production, Hack AG
FAQ
Cobot palletizing doesn’t just meet safety standards—it improves workplace safety. Manual palletizing leads to fatigue and injury from repetitive lifting and awkward postures. Automating with cobots eliminates these risks while built-in safety features like force detection, collision prevention, and controlled speeds keep operations secure.
For more information, download our ergonomics ebook
We’ve designed our solutions for reliability—standardized hardware, smart software, and fast installation keep downtime to a minimum. If an issue comes up, troubleshooting is simple, and our local support network gets you back up and running fast. Plus, with decentralized palletizing, there’s no single point of failure, so your lines keep moving.
Unlike centralized solutions or industrial palletizers that require extensive conveyor rerouting and reduce operational flexibility, our cobot palletizing solutions keep your lines flexible and resilient. Designed for Lean Robotics, they integrate seamlessly into existing layouts—no extensive modifications needed.
Our advanced control algorithms and tooling deliver higher throughput than other cobot solutions. Unlike rigid "in-a-box" systems, Robotiq’s palletizer scales with you, integrating additional automation as your needs evolve.
And while custom-engineered palletizers require long design cycles, ours offers short lead times and intuitive software, making it easy to add new products or pallet patterns. For more information see our Automated Palletizing Buyer’s Guide.
Our global network of Expert Partners is available to show you a demo. You can even test a Robotiq Palletizing Solution with your own products if you wish! Book a demo with an Expert Partner near you.
The Robotiq team also travels regularly to trade shows to give live demos of the Robotiq Palletizing Solution. Check out our events page to see if we'll be in your area soon!
The Lean Robotics book by Robotiq CEO Samuel Bouchard is the result of a decade of the company’s experience helping thousands of manufacturers overcome production challenges using robots.