When you think about automating a production line, it’s easy to imagine a major investment, a...
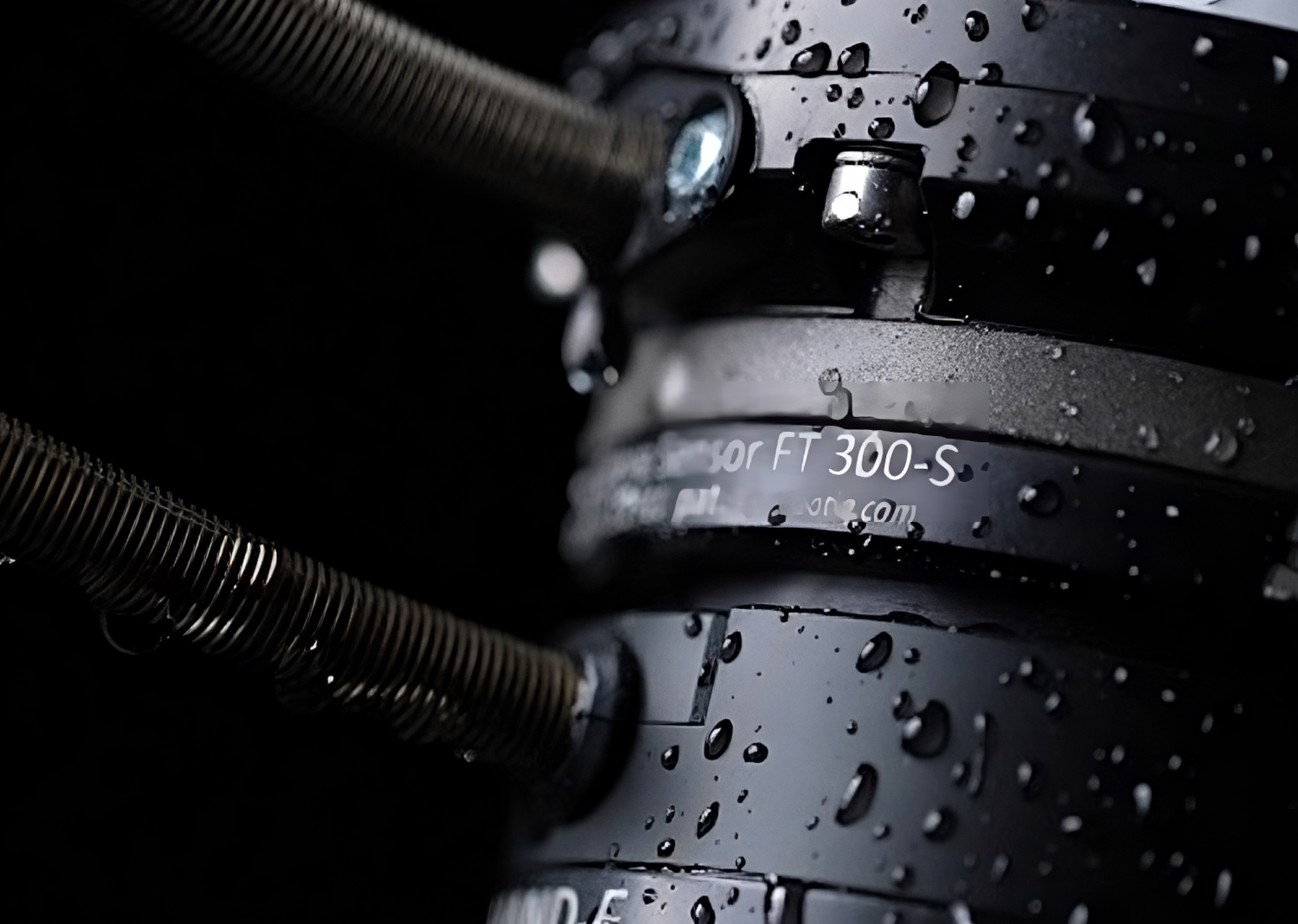
FORCE TORQUE SENSOR
Precision, reliability, and flexibility
Meet the FT 300-S Force Torque Sensor
The FT 300-S is a multi-axis force and torque sensor that enables robots to perform force-sensitive tasks. It precisely detects and measures robot contacts in order to improve the robot control and simplify its programming.
Whether the work takes place in a clean, dirty, or harsh environment, the FT 300-S is designed to check all the boxes.
-
IP65
IP RATING
±300 N
MEASURING RANGE
500%
OVERLOAD CAPACITY
Designed to check all the boxes
Features
Key Features of Hand-E Gripper by Robotiq
Built for collaborative robots
- 50-mm stroke gripper model is suited to collaborative robots
- Integrates seamlessly with Robotiq’s Wrist Camera and FT 300 Force Torque Sensor
- Ergonomic shape for hand-guiding
Built for collaborative robots
- 50-mm stroke gripper model is suited to collaborative robots
- Integrates seamlessly with Robotiq’s Wrist Camera and FT 300 Force Torque Sensor
- Ergonomic shape for hand-guiding
Built for collaborative robots
- 50-mm stroke gripper model is suited to collaborative robots
- Integrates seamlessly with Robotiq’s Wrist Camera and FT 300 Force Torque Sensor
- Ergonomic shape for hand-guiding
Built for collaborative robots
- 50-mm stroke gripper model is suited to collaborative robots
- Integrates seamlessly with Robotiq’s Wrist Camera and FT 300 Force Torque Sensor
- Ergonomic shape for hand-guiding
Integration
Easy to integrate, easy to use
Robotiq’s Hand-E Gripper is simple to integrate in your production environment and easy for workers of all skill levels to use—no robotics experience required.Install your adaptive gripper in just a few minutes, thanks to our Plug + Play gripper kits. Then use our intuitive software interface to program directly on your robot’s touchscreen.
Accelerate your production line
Increase productivity and improve your cycle time with a dual configuration, which lets you handle more objects at a time. The dual Hand-E configuration is the perfect way to keep your CNC machine fed, even when your operators are away.
Accelerate your production line
Increase productivity and improve your cycle time with a dual configuration, which lets you handle more objects at a time. The dual Hand-E configuration is the perfect way to keep your CNC machine fed, even when your operators are away.
Accelerate your production line
Increase productivity and improve your cycle time with a dual configuration, which lets you handle more objects at a time. The dual Hand-E configuration is the perfect way to keep your CNC machine fed, even when your operators are away.
Technical Documentation
Gorem ipsum dolor sit amet, consectetur adipiscing elit.
Robotiq has a variety of technical information available for your solution.
Specifications
Morem ipsum dolor sit amet
Qorem ipsum dolor sit amet, consectetur adipiscing elit. Nunc vulputate libero et velit interdum, ac aliquet odio mattis.
Stroke 50 mm (2.0 in) Stroke 50 mm (2.0 in) Stroke 50 mm (2.0 in) Stroke 50 mm (2.0 in) Stroke 50 mm (2.0 in) Stroke 50 mm (2.0 in) Stroke 50 mm (2.0 in) *Calculated for the use of silicon covered fingertips to grip a steel object, at a low robot acceleration.
-
6500
Cases palletized in a day
6500
Cases palletized in a day
6500
Cases palletized in a day
Applications
Versatile Applications of Hand-E Grippers by Robotiq
Quality Testing
Read more
Quality Testing
Read more
Quality Testing
Read more
Quality Testing
Read more
Quick installation
- Compact design for easy coupling.
- Plug & play integration.
- Intuitive and powerful software included (Force Copilot).
- Compatible with Omron TM, Techman Robot, and Universal Robots (CB Series).
- Development Package available for Linux and Windows.
Flexible use cases
- IP65 rating.
- Performs in environments where dust, debris, or water is present.
- Industrial environments.
- Precise object placement, alignment and insertion.
High performance
- Adjustable tool weight based on the center of gravity.
- Sensor value resetting.
- Hand-guided robot movement for complex trajectories.
- Consistent force and stiffness for each axis.
- Takes precise, repeatable, and high-resolution measurements.
Integration
Easy to integrate, easy to use
Robotiq’s Hand-E Gripper is simple to integrate in your production environment and easy for workers of all skill levels to use—no robotics experience required.Install your adaptive gripper in just a few minutes, thanks to our Plug + Play gripper kits. Then use our intuitive software interface to program directly on your robot’s touchscreen.
Accelerate your production line
Increase productivity and improve your cycle time with a dual configuration, which lets you handle more objects at a time. The dual Hand-E configuration is the perfect way to keep your CNC machine fed, even when your operators are away.
Accelerate your production line
Increase productivity and improve your cycle time with a dual configuration, which lets you handle more objects at a time. The dual Hand-E configuration is the perfect way to keep your CNC machine fed, even when your operators are away.
Accelerate your production line
Increase productivity and improve your cycle time with a dual configuration, which lets you handle more objects at a time. The dual Hand-E configuration is the perfect way to keep your CNC machine fed, even when your operators are away.
Technical Documentation
Gorem ipsum dolor sit amet, consectetur adipiscing elit.
Robotiq has a variety of technical information available for your solution.
Specifications
Morem ipsum dolor sit amet
Qorem ipsum dolor sit amet, consectetur adipiscing elit. Nunc vulputate libero et velit interdum, ac aliquet odio mattis.
Stroke 50 mm (2.0 in) Stroke 50 mm (2.0 in) Stroke 50 mm (2.0 in) Stroke 50 mm (2.0 in) Stroke 50 mm (2.0 in) Stroke 50 mm (2.0 in) Stroke 50 mm (2.0 in) *Calculated for the use of silicon covered fingertips to grip a steel object, at a low robot acceleration.
-
6500
Cases palletized in a day
6500
Cases palletized in a day
6500
Cases palletized in a day
Applications
Versatile Applications of Hand-E Grippers by Robotiq
Quality Testing
Read more
Quality Testing
Read more
Quality Testing
Read more
Quality Testing
Read more
Features
Key Features of Hand-E Gripper by Robotiq
Built for collaborative robots
- 50-mm stroke gripper model is suited to collaborative robots
- Integrates seamlessly with Robotiq’s Wrist Camera and FT 300 Force Torque Sensor
- Ergonomic shape for hand-guiding
Built for collaborative robots
- 50-mm stroke gripper model is suited to collaborative robots
- Integrates seamlessly with Robotiq’s Wrist Camera and FT 300 Force Torque Sensor
- Ergonomic shape for hand-guiding
Built for collaborative robots
- 50-mm stroke gripper model is suited to collaborative robots
- Integrates seamlessly with Robotiq’s Wrist Camera and FT 300 Force Torque Sensor
- Ergonomic shape for hand-guiding
Built for collaborative robots
- 50-mm stroke gripper model is suited to collaborative robots
- Integrates seamlessly with Robotiq’s Wrist Camera and FT 300 Force Torque Sensor
- Ergonomic shape for hand-guiding
Increase cobot cell reliability and flexibility
The FT 300-S Force Torque Sensor takes precise, repeatable, and high-resolution measurements. This plug-and-play tool increases cobot cell capabilities—adding dexterity, flexibility, and reliability—in assembly, insertion, pick-and-place, finishing, quality testing, and machine-tending applications.
Designed for high performance
The FT 300-S Sensor’s stiff metal composition and wear-free sensing technology ensure high accuracy and repeatability. The sensing technology also means no calibration is needed during the life of the product. No calibration means no production downtime!
Streamlined integration
Installation of the Robotiq FT 300-S is done without having to do manual configuration, and without extensive robotics knowledge. With plug-and-play integration, this tool makes configurations easy and fast. It also comes equipped with powerful and intuitive software (Force Copilot).
Reliable operations
The Force Torque Sensor software (Force Copilot) lets users at all levels of robotics expertise quickly set up force-sensitive tasks. The software captures the users’ parameters and executes complex force-sensitive tasks without requiring any programming.
Technical Documentation
Gorem ipsum dolor sit amet, consectetur adipiscing elit.
Robotiq has a variety of technical information available for your solution.
Specifications
Morem ipsum dolor sit amet
Qorem ipsum dolor sit amet, consectetur adipiscing elit. Nunc vulputate libero et velit interdum, ac aliquet odio mattis.
Stroke 50 mm (2.0 in) Stroke 50 mm (2.0 in) Stroke 50 mm (2.0 in) Stroke 50 mm (2.0 in) Stroke 50 mm (2.0 in) Stroke 50 mm (2.0 in) Stroke 50 mm (2.0 in) *Calculated for the use of silicon covered fingertips to grip a steel object, at a low robot acceleration.
-
6500
Cases palletized in a day
6500
Cases palletized in a day
6500
Cases palletized in a day
Applications
Versatile Applications of Hand-E Grippers by Robotiq
Quality Testing
Read more
Quality Testing
Read more
Quality Testing
Read more
Quality Testing
Read more
Features
Key Features of Hand-E Gripper by Robotiq
Built for collaborative robots
- 50-mm stroke gripper model is suited to collaborative robots
- Integrates seamlessly with Robotiq’s Wrist Camera and FT 300 Force Torque Sensor
- Ergonomic shape for hand-guiding
Built for collaborative robots
- 50-mm stroke gripper model is suited to collaborative robots
- Integrates seamlessly with Robotiq’s Wrist Camera and FT 300 Force Torque Sensor
- Ergonomic shape for hand-guiding
Built for collaborative robots
- 50-mm stroke gripper model is suited to collaborative robots
- Integrates seamlessly with Robotiq’s Wrist Camera and FT 300 Force Torque Sensor
- Ergonomic shape for hand-guiding
Built for collaborative robots
- 50-mm stroke gripper model is suited to collaborative robots
- Integrates seamlessly with Robotiq’s Wrist Camera and FT 300 Force Torque Sensor
- Ergonomic shape for hand-guiding
Integration
Easy to integrate, easy to use
Robotiq’s Hand-E Gripper is simple to integrate in your production environment and easy for workers of all skill levels to use—no robotics experience required.Install your adaptive gripper in just a few minutes, thanks to our Plug + Play gripper kits. Then use our intuitive software interface to program directly on your robot’s touchscreen.
Accelerate your production line
Increase productivity and improve your cycle time with a dual configuration, which lets you handle more objects at a time. The dual Hand-E configuration is the perfect way to keep your CNC machine fed, even when your operators are away.
Accelerate your production line
Increase productivity and improve your cycle time with a dual configuration, which lets you handle more objects at a time. The dual Hand-E configuration is the perfect way to keep your CNC machine fed, even when your operators are away.
Accelerate your production line
Increase productivity and improve your cycle time with a dual configuration, which lets you handle more objects at a time. The dual Hand-E configuration is the perfect way to keep your CNC machine fed, even when your operators are away.
Technical Documentation
Gorem ipsum dolor sit amet, consectetur adipiscing elit.
Robotiq has a variety of technical information available for your solution.
Specifications
Morem ipsum dolor sit amet
Qorem ipsum dolor sit amet, consectetur adipiscing elit. Nunc vulputate libero et velit interdum, ac aliquet odio mattis.
Stroke 50 mm (2.0 in) Stroke 50 mm (2.0 in) Stroke 50 mm (2.0 in) Stroke 50 mm (2.0 in) Stroke 50 mm (2.0 in) Stroke 50 mm (2.0 in) Stroke 50 mm (2.0 in) *Calculated for the use of silicon covered fingertips to grip a steel object, at a low robot acceleration.
-
6500
Cases palletized in a day
Supporting documentation for a seamless experience
Features
Key Features of Hand-E Gripper by Robotiq
Built for collaborative robots
- 50-mm stroke gripper model is suited to collaborative robots
- Integrates seamlessly with Robotiq’s Wrist Camera and FT 300 Force Torque Sensor
- Ergonomic shape for hand-guiding
Built for collaborative robots
- 50-mm stroke gripper model is suited to collaborative robots
- Integrates seamlessly with Robotiq’s Wrist Camera and FT 300 Force Torque Sensor
- Ergonomic shape for hand-guiding
Built for collaborative robots
- 50-mm stroke gripper model is suited to collaborative robots
- Integrates seamlessly with Robotiq’s Wrist Camera and FT 300 Force Torque Sensor
- Ergonomic shape for hand-guiding
Built for collaborative robots
- 50-mm stroke gripper model is suited to collaborative robots
- Integrates seamlessly with Robotiq’s Wrist Camera and FT 300 Force Torque Sensor
- Ergonomic shape for hand-guiding
Integration
Easy to integrate, easy to use
Robotiq’s Hand-E Gripper is simple to integrate in your production environment and easy for workers of all skill levels to use—no robotics experience required.Install your adaptive gripper in just a few minutes, thanks to our Plug + Play gripper kits. Then use our intuitive software interface to program directly on your robot’s touchscreen.
Accelerate your production line
Increase productivity and improve your cycle time with a dual configuration, which lets you handle more objects at a time. The dual Hand-E configuration is the perfect way to keep your CNC machine fed, even when your operators are away.
Accelerate your production line
Increase productivity and improve your cycle time with a dual configuration, which lets you handle more objects at a time. The dual Hand-E configuration is the perfect way to keep your CNC machine fed, even when your operators are away.
Accelerate your production line
Increase productivity and improve your cycle time with a dual configuration, which lets you handle more objects at a time. The dual Hand-E configuration is the perfect way to keep your CNC machine fed, even when your operators are away.
Technical Documentation
Gorem ipsum dolor sit amet, consectetur adipiscing elit.
Robotiq has a variety of technical information available for your solution.
Specifications
Morem ipsum dolor sit amet
Qorem ipsum dolor sit amet, consectetur adipiscing elit. Nunc vulputate libero et velit interdum, ac aliquet odio mattis.
Stroke 50 mm (2.0 in) Stroke 50 mm (2.0 in) Stroke 50 mm (2.0 in) Stroke 50 mm (2.0 in) Stroke 50 mm (2.0 in) Stroke 50 mm (2.0 in) Stroke 50 mm (2.0 in) *Calculated for the use of silicon covered fingertips to grip a steel object, at a low robot acceleration.
-
6500
Cases palletized in a day
6500
Cases palletized in a day
6500
Cases palletized in a day
Applications
Versatile Applications of Hand-E Grippers by Robotiq
Quality Testing
Read more
Quality Testing
Read more
Quality Testing
Read more
Quality Testing
Read more
Features
Key Features of Hand-E Gripper by Robotiq
Built for collaborative robots
- 50-mm stroke gripper model is suited to collaborative robots
- Integrates seamlessly with Robotiq’s Wrist Camera and FT 300 Force Torque Sensor
- Ergonomic shape for hand-guiding
Built for collaborative robots
- 50-mm stroke gripper model is suited to collaborative robots
- Integrates seamlessly with Robotiq’s Wrist Camera and FT 300 Force Torque Sensor
- Ergonomic shape for hand-guiding
Built for collaborative robots
- 50-mm stroke gripper model is suited to collaborative robots
- Integrates seamlessly with Robotiq’s Wrist Camera and FT 300 Force Torque Sensor
- Ergonomic shape for hand-guiding
Built for collaborative robots
- 50-mm stroke gripper model is suited to collaborative robots
- Integrates seamlessly with Robotiq’s Wrist Camera and FT 300 Force Torque Sensor
- Ergonomic shape for hand-guiding
Integration
Easy to integrate, easy to use
Robotiq’s Hand-E Gripper is simple to integrate in your production environment and easy for workers of all skill levels to use—no robotics experience required.Install your adaptive gripper in just a few minutes, thanks to our Plug + Play gripper kits. Then use our intuitive software interface to program directly on your robot’s touchscreen.
Accelerate your production line
Increase productivity and improve your cycle time with a dual configuration, which lets you handle more objects at a time. The dual Hand-E configuration is the perfect way to keep your CNC machine fed, even when your operators are away.
Accelerate your production line
Increase productivity and improve your cycle time with a dual configuration, which lets you handle more objects at a time. The dual Hand-E configuration is the perfect way to keep your CNC machine fed, even when your operators are away.
Accelerate your production line
Increase productivity and improve your cycle time with a dual configuration, which lets you handle more objects at a time. The dual Hand-E configuration is the perfect way to keep your CNC machine fed, even when your operators are away.
Technical Documentation
Gorem ipsum dolor sit amet, consectetur adipiscing elit.
Robotiq has a variety of technical information available for your solution.
Force Torque Sensor
Tooling weight 0.44 kg (1 lb) Measuring range 300 N (FX, FY, FZ) / ± 30 Nm (MX, MY, MZ) Overload capacity 500% External noise sensitivity Immune Data output rate 100 Hz Ingress protection (IP) rating IP65 Operating temperature 15 to 35°C (59 to 95 °F) Cobot compatibility Omron, Techman Robot, Universal Robots -
6500
Cases palletized in a day
6500
Cases palletized in a day
6500
Cases palletized in a day
The Force torque sensor is compatible with the following cobot brands
Features
Key Features of Hand-E Gripper by Robotiq
Built for collaborative robots
- 50-mm stroke gripper model is suited to collaborative robots
- Integrates seamlessly with Robotiq’s Wrist Camera and FT 300 Force Torque Sensor
- Ergonomic shape for hand-guiding
Built for collaborative robots
- 50-mm stroke gripper model is suited to collaborative robots
- Integrates seamlessly with Robotiq’s Wrist Camera and FT 300 Force Torque Sensor
- Ergonomic shape for hand-guiding
Built for collaborative robots
- 50-mm stroke gripper model is suited to collaborative robots
- Integrates seamlessly with Robotiq’s Wrist Camera and FT 300 Force Torque Sensor
- Ergonomic shape for hand-guiding
Built for collaborative robots
- 50-mm stroke gripper model is suited to collaborative robots
- Integrates seamlessly with Robotiq’s Wrist Camera and FT 300 Force Torque Sensor
- Ergonomic shape for hand-guiding
Integration
Easy to integrate, easy to use
Robotiq’s Hand-E Gripper is simple to integrate in your production environment and easy for workers of all skill levels to use—no robotics experience required.Install your adaptive gripper in just a few minutes, thanks to our Plug + Play gripper kits. Then use our intuitive software interface to program directly on your robot’s touchscreen.
Accelerate your production line
Increase productivity and improve your cycle time with a dual configuration, which lets you handle more objects at a time. The dual Hand-E configuration is the perfect way to keep your CNC machine fed, even when your operators are away.
Accelerate your production line
Increase productivity and improve your cycle time with a dual configuration, which lets you handle more objects at a time. The dual Hand-E configuration is the perfect way to keep your CNC machine fed, even when your operators are away.
Accelerate your production line
Increase productivity and improve your cycle time with a dual configuration, which lets you handle more objects at a time. The dual Hand-E configuration is the perfect way to keep your CNC machine fed, even when your operators are away.
Technical Documentation
Gorem ipsum dolor sit amet, consectetur adipiscing elit.
Robotiq has a variety of technical information available for your solution.
Specifications
Morem ipsum dolor sit amet
Qorem ipsum dolor sit amet, consectetur adipiscing elit. Nunc vulputate libero et velit interdum, ac aliquet odio mattis.
Stroke 50 mm (2.0 in) Stroke 50 mm (2.0 in) Stroke 50 mm (2.0 in) Stroke 50 mm (2.0 in) Stroke 50 mm (2.0 in) Stroke 50 mm (2.0 in) Stroke 50 mm (2.0 in) *Calculated for the use of silicon covered fingertips to grip a steel object, at a low robot acceleration.
Customers stories
Gorem ipsum dolor sit amet, consectetur adipiscing elit.
See how the 2-Finger Adaptive Robot Gripper helped triple Voodoo Manufacturing's 3D printing production
The ROI was a slam dunk from the beginning, from how much labor it saved. The installation process was the smoothest install of any piece of equipment I have had to experience in 28 years.
Greg Thayer
Vice-President, Cascade
coffee
The Iron Man Challenge
Norem ipsum dolor sit amet, consectetur adipiscing elit. Etiam eu turpis molestie, dictum est a, mattis tellus. Sed dignissim, metus nec fringilla accumsan, risus sem sollicitudin lacus, ut interdum tellus elit sed risus. Maecenas eget condimentum velit, sit amet feugiat lectus.
Class aptent taciti sociosqu ad litora torquent per conubia nostra, per inceptos himenaeos. Praesent auctor purus luctus enim egestas, ac scelerisque ante pulvinar.Specifications
Morem ipsum dolor sit amet
Qorem ipsum dolor sit amet, consectetur adipiscing elit. Nunc vulputate libero et velit interdum, ac aliquet odio mattis.
Stroke 50 mm (2.0 in) 50 mm (2.0 in) 50 mm (2.0 in) Stroke 50 mm (2.0 in) 50 mm (2.0 in) 50 mm (2.0 in) Stroke 50 mm (2.0 in) 50 mm (2.0 in) 50 mm (2.0 in) Stroke 50 mm (2.0 in) 50 mm (2.0 in) 50 mm (2.0 in) Stroke 50 mm (2.0 in) 50 mm (2.0 in) 50 mm (2.0 in) Stroke 50 mm (2.0 in) 50 mm (2.0 in) 50 mm (2.0 in) Stroke 50 mm (2.0 in) 50 mm (2.0 in) 50 mm (2.0 in)
Other components